论文部分内容阅读
At the upcoming ITMA 2019, China Hi-Tech Group Corporation is to bring its subordinate companies Jingwei Intelligent Textile Machinery Co., Ltd., Beijing Jingwei Textile Machinery New Technology Co., Ltd., Yichang Jingwei Textile Machinery Co., Ltd., and China Textile Science and Technology Development Co., Ltd. to showcase a wide variety of equipment.
Jingwei Intelligent Textile Machinery Co., Ltd.
At the exhibition, Jingwei Intelligent Textile Machinery Co., Ltd. will mainly promote its JWF1589 New high-speed intelligent series ring spinning machine.
JWF1589 ring spinning machine is a new high-speed intelligent series ring spinning frame developed by Jingwei Intelligent Textile Machinery Co., Ltd. according to the development trend of the current ring spinning machine with the existing mature technology and international advanced structure. The machine adopts modular and industrial integration design. Ring rail plate and yarn guide plate adopt active, stable and positive lifting system which can be equipped with electronic twisting, electronic drafting or mechanical drafting technology, and features of quick installation of entire section packing. Slub-yarn system, compact system, individual spindle broken-end detection system, roving feeding stop device and spandex core-spun yarn device are optional. The machine runs more stably and reliably at 22,000 - 25,000 rpm.
JWF1589 Composition of the machine: JWF1589 highspeed intelligent ring spinning frame with mechanical drafting and JWF1589E high-speed intelligent ring spinning machine with electronic twisting and electronic drafting
Advantages:
High speed in the entire section installation
The modular design of the entire installation technology makes the machine more stable at the speed of 22,000 - 25,000 rpm, and the installation time is greatly shortened.
Active and stable positive lifting system
Ring rail and the yarn guide plate adopt active and stable lifting system,which makes it more stable and reliable in the process of moving up and down at high speed and also avoids problem of ring rail gauge out for a long time.Spinning building is more perfect facilitating to high-speed winder and process parameters adjustment on the operation panel is more precise.
Electronic drafting
Servo-drivers are adopted instead of twist changing gear and total changing gear to realize processing parameter be adjusted on line, which widen the application scope of RSF spinning process. The Max. multiple is over 100 times. Rollers are controlled by high-precision servosystem through pulse follow technology to ensure roller driving synchronously. Energy-saving technology
Energy-saving motor,energy-saving spindle tape, energysaving tension device and energy-saving spindle are adopted.
Auto-doffing system
Stable auto-doffing system is adopted with high reliability.
Electronic twisting
The front roller speed can be adjusted automatically to ensure spindle running synchronously with roller and twist adjusted easily.
Compact spinning system (optional)
Integrated designed four roller compact system can improve yarn hairiness index.
Individual spindle broken-end detection device
Individual spindle speed, broken end, weak twist etc. can be detected precisely and yarn reserving rate, precise production etc. can be counted. And improve efficiency of spinning machine, reduce labor costs and promote operation ability.
Precise doffing-tube counting device
Counting convex disc without tube is fitted in the non-spinning position to avoid empty tube at doffing and reduce workload in winding process.
Electronic braking system
Precise yarn-end reserve, electronic braking and power interruption simultaneously can control brake motion rapidly and precisely, improve yarn reserving rate or avoid yarn-end cleaning. Electronic braking system is necessary for yarn clamping spindle.
Spinning technology expert system
Spinning technology one-key guide function: 10 sets of technology parameter are built in the program. The parameter can be invoked according to spinning varieties. Customer can revise or save the parameters convenient for the customer when changing spinning variety.
Continuous innovation of expanding functions:
Can be fitted with soft and smooth spinning unit and corespun yarn unit;
Roving-spinning combined and spinning-conner combined can be realized;
Colored yarn intelligent spinning controlling system;
On-line monitoring management network system;
Roving feeding stop system.
Beijing Jingwei Textile Machinery New Technology Co., Ltd.
Beijing Jingwei Textile Machinery New Technology Co., Ltd. will mainly exhibit its JWG0101 bobbin yarn automatic packaging system and JINLING (precise execution, flexible configuration) series of foreign fiber sorter.
JWG0101 bobbin yarn automatic packaging system is a full automatic bobbin yarn transportation and packaging system. The functions of automatic yarn loading, automatic transportation, yarn laying, automatic stacking, transplanting and transporting, stacking inspection, automatic film covering, bag opening and bagging, automatic sewing bag, weighing and labeling bag, automatic storage are realized. The automatic package system of bobbin yarn reduces more than 80% of the packaging workers, greatly reduces the labor cost and labor intensity of the employees, at the same time improves the work efficiency, reduces the production energy consumption, and improves the automation and intelligence level of the cotton spinning workshop. The bobbin yarn track conveying system completes taking yarn from the winder belt and conveying the bobbin yarn along the track to the automatic packaging area. The bobbin yarn is conveyed to the packaging area to lower the yarn and enter the automatic packaging line. The system is composed of lifting mechanism, track, suspension chain and yarn lowering mechanism.
The utility model is composed of a drum line and a shuttle truck, and is used for conveying drum yarn stacking and finished product stacking.
Main features:
Automatic yarn-feeding: from winder to air track automatically, and classify the types of memory yarn to realize automatic transport of yarn in air track;
Lower yarn arrangement: The yarn arrangement mechanism is dynamically allocated according to the number and variety of the bobbin yarn on the track to realize the automatic arrangement of the bobbin yarn on the track, and the weight of each bobbin yarn is measured in real time;
Automatic palletizing: automatic palletizing of bobbin yarn is realized by truss robot according to the variety of bobbin yarn;
Transplanting and transporting: the whole stacking yarn can be automatically transported to the packaging system through the drum line;
Palletizing inspection: realizing automatic palletizing and inspection of whole stacked yarn, and realizing inspection and elimination of yarn appearance;
Auto-sealing: realizing auto-covering and film-sealing of bobbin yarn;
Bag opening and bagging: automatic bagging of woven bags and automatic bagging of yarns;
Automatic sewing bags: full-bag drum yarn to achieve automatic sewing bags;
Weighing and labeling bags: automatic weighing, labeling and bundling of whole bag drum yarn;
Automatic warehousing: The whole bag of yarn is automatically coded and transported to the designated position by truss robot and AGV.
At present, it has been installed in Dasheng Textile Group, Nanyang Textile, Shandong Ruyi, Wuxi Longitudinal and Weft Textile Technology Testing Co., Ltd. and Wuxi Longitudinal and Weft Textile Technology Testing Co., Ltd. It has installed 50,000 spindles automatic transportation and packing system as the visiting workshop of this product. Welcome to visit and order from users.
JINLING (precise execution, flexible configuration) series of foreign fiber sorter is the automatic intelligent technology launched by Beijing Jingwei Textile Machinery New Technology Co., Ltd., which inherits the original technology accumulation, summarizes the user’s practical experience, absorbs the latest international technology, and independently innovates. Foreign fiber sorting equipment. He has more than 20 intellectual property rights to date. The equipment is suitable for installation in the process of cleaning and combing, clearing and winding, and ginning process. It can detect all kinds of foreign fibers in cotton in real time and high efficiency, including polypropylene fibers, flax fibers, hair, various color threads, plastic sheets,cloth pieces, polluted cotton, white polypropylene yarn and white threads, plastic films, etc.
The device uses artificial intelligence and large data processing to design recognition algorithms, parallel high-speed image processing architecture, multi-spectral illumination and imaging system (highlighted plastic films, no color, subtle features, etc.), high-speed and efficient ejection execution system (precise execution), Friendly human-machine interface, simple routine maintenance, remote operation and accessibility information collection system, modular selection (flexible configuration) according to customer characteristics. Since it was put on the market in 2003, more than 2,000 sets of equipment have been used to serve cotton spinning enterprises at home and abroad, which has become a powerful guarantee for the high quality of cotton spinning enterprises. The company solemnly promises: the products provide lifelong service, and the high-quality professional service team makes users feel more assured.
Yichang Jingwei Textile Machinery Co., Ltd.
Yichang Jingwei Textile Machinery Co., Ltd. is to exhibit its K3501 direct cabling corder. The series direct cabling corder is mainly used for making 2-ply symmetric tire cords and industrial yarns from the filament such as PA, PET, RAYON etc. this machine is characterized by low energy consumption, less labour, high quality tire cords and large packages. The tire cord can be used for making tire cord fabric, conveyor belt, driving belt, rope etc. It is also suitable for twisting all BCF yarns (PA, PP, PES, PTT, etc.), Continuous synthetic filament yarns (PA, PP, PES, PTT, etc.) , staple fibers, etc.
Main features:
High efficiency: Motor spindle drive, Max. mechanical speed is 11,000 rpm;
High quality: The patent new type cord regulator and hysteresis type inner yarn tensioner and outer yarn tensioner ensure the length consistent between inner yarn and outer yarns after spinning, and control the yarn tension more accurate. Accuracy tension control ensures the stable balloon, which results in high qualified twist;
Intelligent E-system: Realized the networking between machines, remote diagnosis and control; The Hi-lo creel adopt the new type pneumatic structure, easy to load and unload the feeding package;
Low power consumption: Stable outer yarn tension and balloon ensure the better e-saving effect;
Low strength loss: Improve the design of the yarn path parts to reduce the yarn strength loss;
Easy to threading operation by pneumatic method and quick to set the technical data;
High full package rate: Adopt the improved outer yarn tension intelligent control system, lower the yarn end breakage rate, further improve the full package rate;
The machine can be used as direct cabling and TFO twisting when twisting the carpet yarns, easy to change the production mode for the customer.
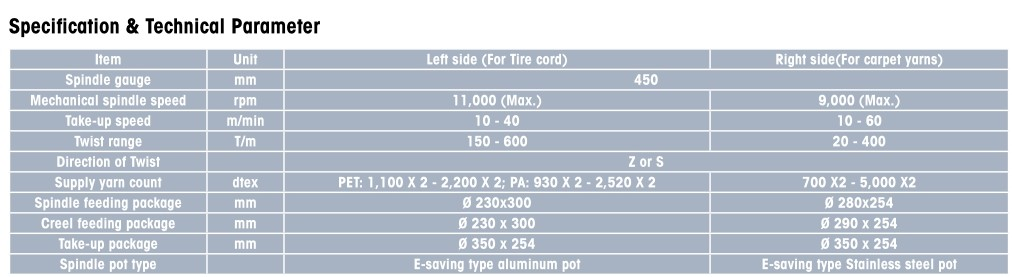
China Textile Science and Technology Co., Ltd.
China Textile Science and Technology Co., Ltd. is to exhibit its 3.2m SSS, 3.2m SMMS, and 3.2m SSMMS, providing you solution of spun-melt nonwovens equipment.
Specifications of 3.2m SSS:
Max. process speed: 600 m/min;
Max. output: 1,650 kg/h;
Weight scope: 8 - 80 gsm;
Fiber fineness: ≤ 1.6 den;
Power consumption per ton fabric: 700 - 900 kwh;
Weight coefficient of variation CV(%): ≤ 1 - 3%;
Elongation at break (%): ≤ 70%.
Specifications of 3.2m SMMS
Max. process speed: 600 m/min;
Max. output: 1,350 kg/h;
Weight scope: 10 - 80 gsm;
SB fiber fineness: ≤ 1.6 den;
MB fiber fineness: 2 - 5 μm;
Power consumption per ton fabric: 1,200 - 1,500 kwh;
Weight coefficient of variation CV(%): ≤ 1 - 3%;
Elongation at break (%): ≤ 75%;
Hydro head (mmH2O): ≥ 180 (13 gsm).
Specifications of 3.2m SSMMS
Max. process speed: 600 m/min;
Max. output: 1,900 kg/h;
weight scope: 10 - 80 gsm;
SB fiber fineness: ≤ 1.6 den;
MB fiber fineness: 2 - 5 μm;
Power consumption per ton fabric: 1,200 - 1,500 kwh;
Weight coefficient of variation CV(%): ≤1 - 3%;
Elongation at break (%): ≤ 75%;
Hydro head (mmH2O): ≥ 180 (13 gsm).
Rieter: Digital spinning as the key to success
Digital Rieter products have one thing in common: They are always focused on the customer. They not only help the decision-making process at management level, but also help employees take the numerous decisions that need to be taken every day in spinning mills, objectively and quickly. Digitalization is making inroads into spinning mills with Rieter Digital Spinning Suite, for example with SPIDERweb. This mill monitoring system records data on processes, quality and production efficiency, analyzes the data, and detects deviations promptly. This allows short response time to introduce the right measures, increases the efficiency of machinery, and reduces the cost of spinning mills. The system is also available for retrofitting on existing machines and equipment.
Rieter customers can monitor the performance of a spinning mill 24/7 from anywhere and respond quickly in critical cases with the Alert and Cock-pit Module for smartphones. It provides the key figures for production, quality and energy in real time.
Thanks to DASHboard, it is now possible to quickly and visibly display relevant key data in the mill. The display unit for spinning mills shows information on a range of factors, such as efficiency, production, quality, or the output of operators. In addition, the correlation between the factors can be shown, and predefined limit values can also be identified.
What if you knew exactly what actions needed to be taken be- fore a machine malfunctioned? With UPtime, the power of prediction is now available.
When it comes to machines and malfunctions, predicting the future could not only help a business avoid downtime, but could also save money, improve quality and increase productivity. Rieter introduces a new approach to machine maintenance with UPtime, an innovation that achieves what was once unimaginable: predicting issues and malfunctions before they happen.
The aim of any maintenance strategy is to minimize downtime and keep production on schedule. A preventive approach uses statistics to determine when maintenance should be executed, but this does not eliminate unexpected downtime and it can also lead to replacing parts before it is necessary to do so. Predictive maintenance is based on past and real-time data, which is analyzed to determine upcoming maintenance requirements.
UPtime collects data and uses artificial intelligence to identify the optimal time to perform maintenance based on a machine’s unique settings and usage. This can lead to cost savings by helping a business evade production interruptions and reduce its stock of spare parts.
Performance-critical information, such as air pressure, temperature and vibration, is transmitted to UPtime through sensors. This data is then used to detect behavior patterns related to potential machine failure. When these patterns occur, UPtime’s artificial intelligence recognizes the likelihood of failure and alerts technicians with early detection warnings and notifications about clear action steps. Furthermore, the system continuously learns from data and patterns, which means that UPtime’s predictive power improves over time. GERON Card Clothing: Exhibiting various products
At ITMA 2019, GERON Card Clothing (Jiangsu) Co., Ltd. brings a variety of products, including Flat top MCBH58, Flat top MCBH40/S, Flat top MCH52/B for Pima cotton, Flat top MCH52/M for superfine fiber, Double mountain cylinder wire AC2040B*1840, Integrate combing roller, 130 degree Circular comb, and Twin stationary flat.
Flat top MCBH58 is suitable for spinning high-impregnated cotton (machine cotton), medium and high 30 or more yarns for carding, combing, ring spinning, and air-jet spinning. Increasing horizontal density and reducing the working angle can improve carding for getting single fiber, less fiber damage, short fiber and neps. Through scientific distribution of the vertical direction, the needle angle can be improved, strengthening the control of the fiber combing flow direction, easy to clean trash and fiber less loading, improving the IPI.
Flat top MCBH40/S suits for synthetic fiber, especially better performance for polyester fiber (1.27-1.68dtex * 38mm). Optimized design to improve the carding and straighten fiber, fiber completely mix and carding; easily to remove the defect hard doubling fiber and less fiber damage. The wire structure and material is more suitable for high speed carding and have excellent performance to puncture fiber and release fiber, with better fiber control and less fiber loading.
Flat top MCH52/B for Pima cotton suits for carding U.S. Pima long cotton, solves the carding problem of increase short fiber and neps because of the high trash, high sugar, long length and thin fineness. It improves the wire life time and get the stability carding quality.
Flat top MCH52/M for superfine fiber is mainly for the carding differential fiber, the fine fiber. 6-1 dtex, less strength, low modulus of elasticity, much static, solve that produce neps because of the fiber easily twine during the carding.
Double mountain cylinder wire AC2040B*1840, according to the carding theoretical model, has the design philosophy: Increase one more small tooth on the back of the tooth, the small tooth will support the fiber and also carding fiber, improve the carding and improve the neps and trash remove efficiency. The sharp teeth design will keep the working surface smoothness, less influence for wire teeth wear resistance.
Integrate combing roller is produced by molding, avoided extra grooved, less intertwine. While working process, air more stable, and fiber transfer smooth, it can improve yarn CV. Through surface coated technology, it will make the roller surface smoother, decrease fiber damage and fiber transfer resistance. Due to diamond coated with high wear resistant, it makes DN coating roller longer life time than normal roller 3 to 5 times, it can reduce customer change roller times and yarn quality worse trouble. Convenience install and change while process different kind of yarn, reduce customer stock. High-precision processing ensures the sharpness, concentricity and consistency of all teeth height, it is high yarn quality effective guarantee. 130 degree Circular comb is featured with high speed & high production, high quality & low waste-cotton, and high spinnability. It suits for high speed and high production, the central angle increasing 18 degree base on 112 degree, it can satisfy the sliver weight 75 - 80 g/m, speed 450 - 500 nips/min high production combing machine. It satisfies customer’s high quality requirements.
Twin stationary flat construction suits for JSC326, JSC330(SC60), JWF1204, JWF1206, JWF1211, JWF1213, DK903, TC11, TC15, C60 high production carding machine, which use double rows wire (different PPSI), wire pitch and PPSI from thin to dense. Compared with the single product, the carding teeth are doubled to improve the carding effect and yarn quality.
Jiangyin Huafang: Displaying various equipment
During the exhibition, Jiangyin Huafang New Technology& Science Research Co., Ltd. is to exhibit various equipment, including HF928B high speed automatic sectional warping machine, HFGA158 Direct Warping Machine, HFGT158 Big V Creel, and HFGA136B Ball Warping Machine.
HF928R High Speed Automatic Sectional Warping Machine has wide applications, modular structures and lots of optional parts ensure this machine can warp any staple yarn and filament yarn. Main feature of this machine is the different winding direction which is winding counterclockwise, skein yarn can be put in without opening any roller when warping, guarantee a constant and complete arrangement of warp yarn. Accurate yarn guide motion is achieved by opening type between creel and front reed, without any skein ends. Fully usage of the evener roller (under warping table) guarantees the evenness of yarn section. According to different process when beaming, provide various types of yarn threading which reduce the friction between yarn and middle guide rollers. Beaming tension is controlled more stable by segmented. With displacement auto-measure system and section tension auto-control, computer workstation can store large amount of process parameters. Connecting with customer’s ERP data can be achieved and also connect with mobile APP to monitor machine working condition.
HFGA158 Direct Warping Machine is suitable working with cotton, hemp, polyester and blended fiber, etc... This machine applies Germany-imported encoder to count length, complete set of imported hydraulic components controls the pressure and brake force of press roller, provide guarantee for high efficient production and high quality products. When warping dyed beam, yarn feed roller is equipped with servo motor and laser system, which guarantees dyed beam meets customer’s process, and also equipped with servo controlled load/ unload system to work with different diameters of beam. Connecting with customer’s ERP data can be achieved and also connect with mobile APP to monitor machine working condition. HFGT158 Big V Creel is mainly workable for staple yarn over 32S and any specifications of cones. This creel applies original Switzerland SAURER broken yarn auto-stop detecting device, achieve individual broken yarn detecting, confirm yarn number preview. Auto pre-tensioner can prevent yarn loosen when machine stops, and automatically adjust to correct position according to different stages when warping, unique yarn tensioner guarantees low yarn tension when machine is working in high speed: internal individual blowing device keeps the tensioner clean, unique electric-cut device, cutter can be charged directly, no need other spare batteries.
HFGA136B Ball Warping Machine is workable for rope dyeing process in cotton industry. More user-friendly of load/unload, yarn threading control and vacuum device (dust-remove), unique press guarantees high quality ball, which can also reduce labor intensity and increase environment quality. Mechanical type and servo type of yarn feeding is optional for customers. Connecting with customer’s ERP data can be achieved and also connect with mobile APP to monitor machine working condition.
Ring frame electronic drive control: Simply ring frame constructure, cancel original main motor and wharve, so can remove the air flow influence caused by many wharve high speed running and reduce the noise. Spindle can drive seperately, set spinning twist directly, no need to change machinery parts and easy operation.Install the PCB board on keel, control each spindle running, easy erectionYarn breakage detection device, after yarn breakage, roving stop automatically, reduce waste, save energy sharply.
Qingdao Hicorp Group: Focusing on intelligent equipment
During the exhibition, Qingdao Hicorp Group will display a variety of production with original technologies, including HCP2025 Intelligent Roving Frame and Finished Woven Bags Automatic Packaging system.
The latest generation of intelligent roving Frame designed by Chinese and foreign experts team of Qingdao Hicorp Group for 10 years. The world’s first technology has subverted the traditional structure of the roving frame, broken through the bottleneck of the original structure, increased double spindles than original longest spindle (216 spindles) and made the operation more intelligent.
The main features:
The max spindle is up to 432 spindles;
Suitable for multi-varieties spinning;
The patent waste roving recycling system, recycling by variety, improve recycling efficiency; The electronic drafting, cancel all process gears;
Expert database system makes spinning easier;
Two different varieties can be spun at the same time, and the variety combination is more flexible;
Less area occupied, less labor requested;
Perfect connection between Hicorp Cloud and remote operation and maintenance system.
Finished Woven Bags Automatic Packaging system realizes unmanned automatic packaging. It has the function of automatic testing of bag pocket and automatic arrangement packing, which effectively solves the problem of automatic packaging with reliable sewing and compact filling of cone yarn.
The advantages:
Woven bag pattern: Finished woven bag;
Woven bag specifications: length ≤ 1,350, width ≤ 800;
Cone yarn arrangement: 3 * 4, 3 * 5, 2 * 4;
Bag load: Automatic;
Bag open: Automatic;
Bag support: Automatic;
Bag pocket finishing: Automatic;
Bag pocket sewing: Automatic;
Whole bag cone yarn delivery: Automatic;
Cone yarn arrange into bag: Automatic;
Yarn breakage check: Included;
Tight cone yarn bag arrange: Included.
Rizhao YUHUA Machinery: For high-quality component of textile, service forever
Rizhao YUHUA Machinery Co., Ltd. is to exhibit YUHUA brand series top arm, compact, and rings.
“YUHUA” brand top arm have been developed and produced since the end of 1980s. At present, it has achieved the sales of 30 million spindles in textile markets. YUHUA brand series top arm has four series of V-type draft, flat draft, compact spinning special top arm and spring arm. The pendulum arm has the characteristic of accurate pressure regulation, no spring fatigue, small spindle differences, high parallelism, excellent spinning. The product has large pressure regulation range, wide range of products suitable for spinning. The semi-release pressure canbe achieved during the holiday, no need to raise the arm, the rate of yarn breakage is lower when re-starting, high production efficiency.
“YUHUA” compact (be negative pressure four roller compact device) adopts special energy saving fan with low energy consumption. Open-type condensing system for easy maintenance. Torsion spring tension frame makes it easy to disassemble and assemble the lattice circle. The wear-resistant cover provides long service lift and convenient switching between normal spinning and siro spinning. The air flow reverse stop device is convenient for collective exhaust, preventing air flow from pouring backward, and avoiding the large area yarn breakage. The life of roller is double by shifting spinning technology. Cooperative clients (partly) include HENGFENG GROUP, SHANDONG DAHAI, SHANDONG HUAXING, SHANDONG RUYI, LIANFA TEXTILE, SANHE GROUP, CHANGSHAN, SHANDONG HONGYE, BROSS GROUP, HUAFU, YICHENG TIANSHU, XINJIANG XINTAI, etc. “YUHUA” brand rings are characterized by high precision, long life and short ripening period. There are 21 varieties of PG1 and PG1/2, with an annual production capacity of 5 million pieces.
In recent years, the company is committed to the research and development of high-end ring, the current production of high-precision is processed with CNC machine tools, with high dimensional accuracy, consistent internal and external organization and long service life, which is 3 - 5 times of ordinary steel ring, especially suitable for the production and application of compact spinning.
PINTER YUHUA China Technologies Co., Ltd.
At the exhibition, PINTER YUHUA China Technologies Co., Ltd. will showcase EffiSpin, Roving stop device, Spinning software management system, Core yarn, and Fancy spinning system.
Research and development, sales, service together with PINTER FANI, EffiSpin is divided into three series of cotton spinning, wool spinning, siro spinning - electromagnetic type and optical type. This device can collect data in real time, reduce labor, improve production efficiency, is the best choice for company to achieve fine management; it also supports the connection with internet to realize remote real-time monitoring, monitoring the running situation of each spindle; Effispin system used for cotton, Blumis used for wool and Star-Yarn Siro used for Siro.
Roving stop device can reduce roving waste and production labor, eliminate roller winding, reduce the accumulation of bellows, improve production environment, improve yarn quality, reduce energy consumption and save manufacturing cost.
S p i n n i n g software management system can monitor the r e a l - t i m e production infor-mation of the current shift of all machines, conduct data collation and analysis, and view various production data recorded and counted by the system, so as to make the management more reliable and more accurate.
Core yarn can precisely control the tension of the core yarn, automatic traverse,and reduce the loss of the rubber. Core yarn online monitoring can eliminate the empty core yarn and achieve efficient management and perfect control.
Fancy spinning system (come from PINTER CAIPO SAU) can input up to 6 different colors of yarn. Professional software system precisely controls and simulates the feeding of colored cotton yarns.
Brujas: To promote series of high-quality card clothing
Brujas Textile Tech (Shanghai) Co., Ltd. is a Sino-foreign joint venture manufacturer of card clothing. Brujas, founded in 1908 by the Brujas family in Terrassa Spain, has made a joint venture with White Shark Card Clothing Co., Ltd. since 2008. Brujas is a ISO9001 quality approved company and is known as a high quality card clothing product suitable for all carding applications. The main products coverage contains: metallic card clothing, flat tops, stationary flat, integral cylinder, combing roller, cleaning fillet, raising fillet etc., and they are widely used in the areas of cotton spinning, non-woven materials, wool and linen spinning.
In the past 100 years, Brujas has pursued the combination of industry and art, and has been committed to fine production of card clothing as well as the perfect protection of carding material.
Brujas can also provide related textile auxiliary equipment, for example: metallic wire mounting machine, metallic wire weld device, grinding machine, flat clipping machine, flat grinding machine, flat ends milling machine, high precision roller grinding machine, combing roller winding machine etc., and spare parts for textile machine.
Through years of cooperation with White Shark Card Cloth-
ing Co., Ltd., Brujas integrates the advantages in technology, equipment and resource, and produces high-grade card clothing in cooperation with White Shark.
Brujas makes arduous efforts to establish the domestic firstclass enterprise and promote the development of textile industry.
Brujas Textile Tech (Shanghai) Co., Ltd. will mainly recommend OE Wire & Rotor Spinning, Adjustable Stationary Flat, Metallic Card Clothing, Duplex Complete System of Stationary Flat, Flat Tops, etc.
The advantage of OE Wire & Rotor Spinning lies in super wear-resistant and long-life. The main characteristics of Adjustable Stationary Flatde are as follows: high wear-resistant, nonblocked, high anti-rolling, the tooth flatness is less than 0.05 mm, easy to install and adjust. The advantage of Metallic Card Clothing lies in soft combing to protect fiber, beneficial to improve the yarn strength.
Duplex Complete System of Stationary Flat is mainly featured by double rack to strengthen combing, special design with strong self-cleaning, and easy to install and adjust. Flat Tops are characterized by perfect combing channel and high removal efficiency of neps and impurities.
NYBELT CO.: Focusing on various belts and roller coverings
Jinan Tianqi Technical Belts Co., Ltd. (NYBELT CO.), founded in 1990, is one of the largest manufacturers of flat belts in the world. With the total investment of over US$40 million NYBELT possesses the world first-class production lines of nylon sheets, coating, rubber processing, calendering, laminating, leather-processing, transport bands, end-jointing and testing. NYBELT employs over 180 staff and workers including more than 70 of professionals and technicians, the core members of whom were systematically trained abroad both in theory and practice regarding flat belts production, research and development in belting technology, quality control, machinery operation and maintenance as well as after-service. NYBELT produces a wide range of high-efficiency transmission flat belts, tangential belts, spindle tapes, conveyor belts, roller coverings, transport bands, leather belts, nylon sheets and synchronous belts, which are widely used in textile machinery, paper-making, folder-gluer, graphic arts, wood-processing, leatherprocessing, food and tobacco processing, post sorting and others.
NYBELT’s products are popular not only in China but also abroad. It has become well known for providing excellence in service to the customers throughout the world. NYBELT name is backed by 24-hour-a-day service.
With the R&D center of state level, NYBELT has received numerous titles and awards for the progress and development in belting technology. Extensive research and development enables NYBELT continuously put out up-to-date products and keep its leading role in the trade.
NYBELT has gained the certificate of conformity of quality system certification and adopted ISO9001 Standard for its production and servicing of technical belts and nylon sheets.
At ITMA 2019, NYBELT CO. is to exhibit various products, including NYCO? transmission flat belts, NYCO? TE belts, and NYCO roller coverings.
NYCO? transmission flat belts structure consists of friction covers made of special synthetic rubber with high resistance to abrasion or chrome leather; nylon core layer of high tensile strength. Such structure enables the belt to have excellent comprehensive properties: Long service life; Transmission efficiency: over 98%; Transmission speed: over 60 m/s; Good flexibility and directionality; Good dimensional stability; Constant friction coefficient.
NYCO? TE belts are made up of super-high tensile strength PET fabrics and the best kinds of thermoplastic polymers, and the belt surface is component of XNBR with the high abrasion resistance and constant grip. So these TE belts have the characters of high efficiency, energy saving, outstanding dimensional stability, and long service life. They are widely used in various machineries with high speed and shorter tension devices, being unaffected by fluctuation ambient environment. NYCO? TE belts have been recognized by insides as one of the most excellent up to-date power transmission belts in world.
NYCO? roller coverings are designed for increasing coefficient of friction, which can be used in various processing stages of textile industry such as being used in water-jet, air-jet, rapier, projectile looms, fabric inspection machines and dyeing & printing machines by way of wrapping their fabric guide rollers. NYCO roller coverings have various kinds of surface textural designs. With the advantages of wear-resistance, no deformation, no longation, no stripping and durability they are designed for drawing all kinds of fabrics. Rifa Textile Machinery: Exhibiting four high-efficiency & low-consumption equipment
As a national key high-tech enterprise, Zhejiang Rifa Textile Machinery Co., Ltd. has always been market-oriented, focusing on the development of textile machinery technology, specializing in the production of textile machinery, and has successfully developed hundreds of products in four systems: twisting, spinning, weaving and knitting. Now it owns Shandong Rifa Textile Machinery Co., Ltd., Anhui Rifa Textile Machinery Co., Ltd. and Zhejiang Rifa Textile Machinery Technology Co., Ltd. At this exhibition, Rifa Textile Machinery will exhibit RS30D rotor spinning machine, crosrol cleaning comb, RFTL62 high-speed rapier towel loom, and RFJA40 high-speed air jet loom.
RS30D Rotor Spinning Machine
RS30D is an intelligent semi-automatically high-speed rotor spinning machine, integrated with technologies of a new advanced spinning unit, semi-automatic piecing device, automatic doffing, automatically cleaning spin box, Internet of things, electronic servo transverse and single independent drive, as well as electronic micro-switch etc. It opens a new world of semi-automatic air-flow spinning machine with higher production, lower power consumption and better user experience. Service anywhere anytime.
Crosrol Blowing-Carding
The equipment enjoys a balance between higher output and quality, featured with less space, low energy consumption, easy operation, and easy m a i n t e -nance. It is embodied in automatic repiece, automatic gauge adjustment, steel ball support, flat drive, short, medium and long auto-leveling, etc., with high cost performance.
RFTL62 High Speed Rapier Towel Loom
The device is directly driven by the new switched reluctance motor, consequently with an obvious power saving effect; the optimized conjugate cam tightening weft and the “space crankshaft and connecting rod” mechanism, with the new type weft insertion, greatly reducing the head and belt of rapier wear. The optimized towel let-off system ensures that the warp tension is the same, and the woolen loop is smooth and uniform.
RFJA40 High Speed Air-jet Loom
RFJA40 High Speed Air-jet Loom is characterized by highspeed and efficiency, energy saving and low consumption, high automation etc. With the lower center of gravity of the loom, the new dynamical balancing of beating-up mechanism effectively reduces the vibration of loom and at the same time the beating-up force is increased; the further optimization of the 4 - 6 connecting rod beating-up mechanism is more suitable for high speed weaving; the servo motor is used directly to drive the loom. It is obvious in energy saving and convenient for maintenance. Qingdao Haijia Machinery: Promoting three looms
Founded in 2001, Qingdao Haijia Machinery Co., Ltd. is a professional shuttleless looms manufacturing enterprise integrating R&D, manufacturing, sales, international trade and service.
The company attaches importance to the management of independent intellectual property rights, enjoying a total of 52 independent intellectual property rights.
In May 2019, the HW-8010 High-speed and High-density Water Jet Loom developed by the company passed the scientific and technological achievements appraisal. The experts agreed that the result is independent and innovative, and the overall technology has reached the international advanced level.
At ITMA 2019, Qingdao Haijia mainly promotes its HA9010-190-C6 High-speed Air Jet Loom, HW5012-190-P4 Water Jet Loom, and HW8010-230-D10 New High-speed and High-density Water Jet Loom.
HA9010-190-C6 High-speed Air Jet Loom is another new air jet loom developed by Haijia on the basis of HJA-N. The structure of left and right wallboard is beneficial to the production and manufacturing, so that the equipment will be more stable; Optimized design of the shape and position of the four supports makes the loom frame more stable; Improved beating mechanism makes the beating process more balanceable and stable during the operation. The structure of the back beam is improved to make the let-off more uniform and the tension more balanceable, which can reduce errors and improve the rate of high-quality production.
HW5012-190-P4 Water Jet Loom is deeply optimized on the basis of HW4010-190-P4, and the major improvements are: Multiple reinforcement measures are adopted for the machine to maintain a good stability during the high-speed and high-density weaving; Optimal design of weft insertion system improves the efficiency and can fit high-speed insertion; In the optimization of beating system, U shaped beating shaft and special beating balancing system are adopted. Solid beating shaft adopts reinforcement of supporting seat and centralized lubrication system, which improves the beating force and wear condition, increases the service life of the machine. This machine adopts servo direct drive motor, the energy saving effect can reach 25% - 30%.
HW8010-230-D10 New High-speed and High-density Water Jet Loom is deeply optimized on the basis of HW4012-190-P4, and the major improvements are: Adopt the integrated wallboard to optimize the design of the frame part, further improve the stability, efficiency and fabric quality; Reduce the height of the wallboard to make the operation of the loom more user-friendly; The beating method can be either four-bar or six-bar, which is suitable for different fabric requirements; Suitable for wide and high-density fabrics. Based on ultra-highspeed performance and designed with a maximum speed of 1,200 rpm/min, the machine is widely used in weaving fine denier, high-density and high-speed fabrics.
Niupai Textile Machinery: Promoting various shedding devices
At ITMA 2019, Niupai Textile Machinery will exhibit its NP4421 top-mounted positive shedding device, NP5400B highspeed electronic dobby, NP6016 electronic jacquard shedding device, and top-mounted high-speed positive cam shedding device.
NPW408D, whose frame box adopts integral structure, is top-mounted high-speed positive cam shedding device. With the property of strong rigidity, high manufacturing precision, excellent conjugacy, the device is equipped with U-shape steel beam and fully enclosed cover,which reinforces strength,safety as well as anti-corrosion performance and extends the service life of parts effectively. It can meet the weaving requirement of high speed and heavy duty fabric.
Technical Parameters
Reed space: 190 cm - 280 cm;
Max. RPM: 900 rpm (4/1weave, 190 reed space);
Heald frame spacing: 14 mm.
NP5600 Electronic Doddy is low-positioned intelligent positive shedding device that applies to wide and fast speed air-jet looms. Multiple cam curves are provided for weaving different fabrics. It’s characterized by its compact structure, easy operation and large capacity. Its oil filter can sift the fibers within housing.
Reed space: 190 cm - 360 cm;
Max. RPM: 750 rpm (190 cm reed space);
Heald frame spacing: 12 mm;
Shedding unit: 16 pcs;
Spec. of wire: 330 mm;
Shedding amount: 55 mm-160 mm;
Weft picks: 12800 picks.
NP5400B high-speed electronic dobby is top-mounted intelligent positive shedding device. The lubrication oil is forced to circulate via oil pump, and oil level sensor is adopted to avoid lacking oil. It’s characterized by compact structure and easy operation. Thus, it is especially suitable for fast speed and wide unbalanced fabrics. Its energy consumption is 1/3 less than mechanical dobby’s. The device is particularly popular among enterprises with fast changeover of fashion fabrics, short life-cycle and advanced technologies.
Technical Parameters
Reed space: 190 cm - 360 cm;
Max. RPM: 750 rpm (190 cm reed space).
NP6016 electronic jacquard shedding device features longitudinal arrangement of 16 lines of components. With the advantages of compact structure, light weight and robustness, the device can meet the needs of high speed running. NP6016 is equipped with electrical self-check function. It’s capable of weaving tie, trademarks, towels, clothing fabric and lining. Technical Parameters
Specification: 1408, 2816, 3072, 4096, 5120, 5376;
Max RPM: 650 rpm (based on process of fabric weave);
Shedding amount: 46 mm - 130 mm;
Full load of hook ≤ 2,000 kg.
Wuxi Hongyuan: Focusing on high-speed intelligent products
Wuxi Hongyuan Electromechanical Technology Co., Ltd. is highlighted on various intelligent products, including HY-9 Automatic Doffing High-Speed Draw Texturing Machine, HY-10 Multi-Spindle High-Speed Draw Texturing Machine, HY-Auto498 Auto Doffing Roving Frame, and HY-IDS Synthetic Filament Bobbin Automatic Handing System.
HY-9 Automatic Doffing High-Speed Draw Texturing Machine has the characteristics of high automatic level, energy saving, high speed and efficiency, easy operation, etc.
It is featured with total 384 spindles per machine, multi spindles, large production output capacity. Take-up device lies both sides of the machine, easy for operation and maintenance. Pneumatic yarn threading device can make sure the yarn threading performance accurately and labor saving as well. Motorizing friction unit, bobbin auto-doffing device, Hongyuan advanced take-up device.
Developed with multi-function, energy saving, easy operation and high efficiency, with independent intellectual property rights, HY-10 Multi Spindles Draw Texturing Machine can meet the current fierce market competition, and lead the fancy yarn making market. Machine capacity and efficiency are doubled.
Under same spindles, this machine area can shorten half of the space, and reduce the investment.
To achieve High Efficiency and Energy saving, High Automation, reduce labor employment and labor intensity, and satisfy the requirement of high level customer, Hongyuan company developed a new model roving frame with Auto Doffing — HYAuto498. The drafting and main drive system maintain the stable and reliability of the mature machine of Hongyuan company. With external auto-doffing structure, automatically fulfil bobbin doffing, bobbin exchange, yarn threading, run the machine. For the whole process, it needs around 2 minutes.
The characteristics of HY-Auto498 Auto doffing Roving Frame include: With reasonable machine layout reliable headstock driving, easy operation, suitable for high speed. Adopt mature control system and driving mode for 4 main drive and drafting system. Auto-doffing structure adopts external whole doffing design combined with double direction-freedom bobbin rail. Auto-doffing time is not limited by the spindle number, around 2 minutes with high efficiency. With multi inverters control synchronously, the auto doffing rate, empty bobbin exchange rate and auto yarn threading rate can reach nearly 100%, reducing at least half of the labor force. With Touch screen as HMI, easily for input technical parameters and yarn tension control and adjust, doffing parameters can adjust flexibly according to user’s requirement. The automatic bobbin doffing and transport system developed by Hongyuan is a special automatic bobbin-handling system for chemical filament yarn production line.
This system can realize the functions of bobbin auto-doffing and transportation. It can improve the automation level of subsequent process of chemical filament yarn production, improve the product quality and reduce the labor cost. To personalized auxiliary filament yarn product automation system, the module can combine freely according to the different requirement. This system has the characteristics of high quality, high efficiency and lower cost and achieve the international advanced level.
Cixing “KNIT TO SHAPE”opens a new textile future
As the world’s leading intelligent knitting equipment solution provider, Cixing will present a milestone design for the industry - KS series “KNIT TO SHAPE” computerized flat knitting machine, at ITMA 2019 in Barcelona, Spain, which will take you into a new world of knitting. Through the “KNIT TO SHAPE” computerized flat knitting machine and sweater automatic stitching linking system to achieve the machine replacement, and supplemented by the information system to transform the traditional production mode to achieve the division of labor across the entire industry chain. Create a C2M, C2B2C win-win ecosystem for the international knit sweater and footwear market.
“KNIT TO SHAPE” is a new type of fully automatic computerized flat knitting machine developed for ten years by the engineers of Ningbo Cixing Co., Ltd. and its subsidiary, Steiger, Switzerland. It brings together the wisdom of the current knitting technology research and development team, uses intelligent manufacturing, intelligent technology and intelligent knitting as the three carriers, and realizes the knit to shape. It eliminates the expensive, timeconsuming and posterior suture, realizes the automatic knitting, and presents the frontier development trend of current computerized flat knitting machine technology with great technological innovation.
The one-yard to shape technology of KNIT TO SHAPE computerized flat knitting machine can simultaneously complete the knitting of the whole sweater and exhibit it directly to the customer in three-dimensional way. This technology eliminates the costly and time-consuming process of linking, which can achieve the “what you see is what you get” knitting of the real 3D programming, making the production more flexible, more efficient, and the coil is more perfect. About Cixing
Ningbo Cixing Co., Ltd. (stock code: 300307) is a leading company in the world’s supplier of intelligent knitting machinery, and the national high-tech enterprise that is committed to improving the level of China’s knitting machinery technology, promoting the development of knitting technology progress, and realizing knitting industry upgrading.
Cixing shares were successfully listed in 2012, the only listed company in the computerized flat knitting machine industry in China, and Cixing has many advanced patents, of which, a number of technologies to reach the international advanced level, the level of product technology and quality has always maintained the forefront of the industry. Cixing shares have more than 10 subsidiaries, the innovative R&D products include computerized flat knitting machine, Intelligent Flat Knitting Machine, fully automatic stitching system, automatic ironing machine, industrial robots, service robots, Cixing is a representative enterprise of China’s intelligent equipment.
CHTC FONG’S creates a new era of smart dyeing & finishing
CHTC Fong’s has been committed to the development and manufacturing of dyeing and finishing equipment for more than 50 years. In the past decades, CHTC Fong’s devoted to the development of energy-saving and emission reduction machines and now it becomes the basic conditions for dyeing factories. At ITMA 2019 in Barcelona, Spain from June 20th to 26th, CHTC FONG’S will exhibit a full line of the most advanced and innovative products and technology including the new product- FONG’S TECWIN High Temperature Dyeing Machine, Fong’s ALC - Automatic Liquid Chemical Weighting and Dispensing System, THEN SMARTFLOW, Goller KINT MERC, MONNFONG’s Matex Eco Applicator, XORELLA, and MONFORTS Montex Stenter.
FONG’S TECWIN High Temperature Dyeing Machine
FONG’S TECWIN is designed to satisfy the ever-changing market demands. The reliability and versatility of the machine are improved.
TECWIN is equipped with several patented designs:
Combined Air and Front Spray Nozzle
Standard Feature: Increase the degree of dye liquor interchange before passing through the main nozzle.
Optional Feature: Optional blower is equipped. High pressure aerodynamic flow in spray nozzle is provided to resolve the special fabrics that demand high quality.
Automatic Adjustable Nozzle
Adjustment of nozzle setting is automatically done by means of motor drive system, and hence manual changing of nozzle is not required. Liquor Dispersion Storage Chamber
This is a uniquely design chamber for providing a better liquor dispersion effect.
Upper and Lower Overflow
Lower Overflow: Maintaining pump operation with low water level to prevent disturbance caused by rinsing at a high water level;
Upper Overflow: This is adopted for conventional overflow rinsing function.
Furthermore, the dye liquor separation is specially designed in TECWIN. With the use of the variable loading storage chamber, the dyeing operation can be performed more smoothly and fabric patterns can be more organized, which eventually leads to a lower liquor ratio.
The THEN SMARTFLOW– setting a new standard in jet dyeing
At ITMA 2019 in Barcelona from June 20th - 26th, FONG’S EUROPE, a member of CHTC FONG’S international Group based in Schw?bisch Hall, Germany, will introduce its THEN SMARTFLOW TSF hydraulic high temperature dyeing machine.
The THEN SMARTFLOW TSF is designed to achieve the lowest possible energy and water consumption rates available on the market for jet dyeing, with achievable liquor ratios for a full load up to 300 kg with a reduced kier volume and a liquor ratio down to 1:3.5 for cotton and 1:2.5 for synthetics.
FONG’S EUROPE has a number of patents pending on the innovative new features of this machine, including the SMARTFLOW’s fabric transport design. This is based on a smart, winchless fabric transport system which eliminates the need for a loading rope, and a circular plaiter with programmable rotation speeds which provides full filling of the drop zone.
The chambers can accommodate variable loads in terms of both weight and material type down to 40 kg for extremely flexible processing, and each SMARTFLOW TSF unit can be equipped with up to 8 chambers, in order to fully maximize productivity, while taking up to 40% less floor space than competing systems.
“The newly-developed nozzles and reel-less transport in combination with smart controlled circular plaiting and variable chamber adjustment provide even fabric treatment without en- tanglements and the highest loading capacity with the lowest kier volume,” explains FONG’S EUROPE Sales and Marketing Director Richard Fander.
Another innovation is the new bath preparation unit (BPU) and its patented satellite tank.
“As the process times of jet machines have been continuously optimised over the past few decades, they have required an increasing number of service tanks for dyes, auxiliaries and hot water, adding both expense and additional space requirements,” says Mr. Fander. “Our new BPU and satellite tank, with its automatic dosing and mixing programmes, working in combination with the THEN temperature management system, ensures the recipes are supplied in exact quantities, with dyes and auxiliaries well diluted and heated to the required temperature extremely rapidly.” “The new THEN SMARTFLOW allows fully reproducible processing with the optimized use of raw materials, water and energy, for perfect dyeing every time,” he concludes. “Hydraulically driving the fabric without the use of a transport winch opens the door to reducing the tension during treatment and results in the highest relaxation of stretch and spandex fabrics.”
FONG’S EUROPE will be at stand D101 in Hall 2 at ITMA 2019 with THEN and Goller, and Xorella will be at stand D203 in Hall 6.
GOLLER“GOLLER KNIT MERC”
Goller new knit mercerizing was developed to achieve highest quality mercerizing of knit fabrics with lowest tension and upmost best dimension stability (< 3%) over the fabric width for perfect dyeing results.
This new mercerizing compartment is the result of our consequent R&D developments and follow up of our latest “SINTENSA CYCLONE” drum washing compartments for highest washing efficiency with lowest tension.
Fabric content 8,4 mtr. in impregnation compartment plus 4 mtr. in first chain section which gives a production speed of 25 m/min by 30 sec dipping time.
Dry on wet mercerizing;
Cold or hot mercerizing;
Inlet with scroll roller and slat roller for fabric guidance;
Tandematic uncurler in front of rubberized de-airing roller;
Grooved bottom roller with 320mm;
600mm perforated upper drums;
Automatic tension regulation;
Low liquor content integrated lye tank with circulation and Auto filter;
8ton high efficiency squeezer on exit before chain section;
Cast iron pin chain with edge sensors, Tandematic un-curler and overfeed device;
Driven belt arrangement for fabric support;
Overflow wires incl. circulation and filtering for stabilizing;
5ton squeezer at exit of chain field;
High efficiency Goller “SINTENSA CYCLONE” drum washing compartment with Cyclone Rotor specially designed to create an adjustable under-pressure, for an optimized fabric transport, highest washing efficiency and minimized elongation.
MONFORTS FONG’s Matex Eco Applicator
The conventional process of drying the fabric with wet pick up in Stenter process will cause large heat energy consumption, particularly it needs to heat up and evaporate water from the fabric. Our Eco-Applicator will be different from the tradition way but to be the solution to save the energy from this part of processing.
Minimum liquor application device with driven liquor rollers. The alternative to padding. For energy-conscious and cost-cutting drying. Reduced liquor content for lower remaining liquor in the trough. Universal application: Liquor application to one or two sides or different liquor application on front and reverse side. Applications:
Application of softener for terry fabric;
Over dyeing or finishing of denim fabrics;
Hydrophobing/hydrophiling professional clothing;
Stain-repellent finish of decoration fabrics;
Functionalising (e.g. anti-smell) of outerwear;
Eco Applicator for Knitwear and bi-elastane Woven.
Eco Applicator could be suitable for Knitwear and bi-elastic Wovens.
Technical facts:
Suitable for “wet-in-wet and “dry-in-wet” process;
Permanent fabric weight control;
Add on precisely adjusted based on real fabric weight;
Defined application of e.g. softener;
Reproducible effects;
Same or less chemical consumption;
Less wet pick up – less heating energy required;
Contribution to lowering carbon footprint;
Patent applied system – unique selling point.
MONFORTS Montex Stenter with new improved features
New patented sealing devices at inlet and outlet Monforts“bionic fin?” for less heat loss and improved energy efficiency;
New integrated, modular “Eco Pack” unit for individual configuration with heat recovery module, exhaust air cleaning module, UV-zone module for odor remove. For achieving no visible smoke coming out of the stack;
New energy improved stenter design measures with improved sealing of the chamber and preheating of the combustion air option. All measures together lead to overall reduced energy consumption of the app. 13% (depending on the process);
Smart sensors in the stenter allow monitoring of the complete machine by digital twin. Maintenance can be further optimized and productivity improved: Smart sensors for grease reservoir filling of the stentering chain, Smart sensors for wear of Chain rails, spindles and impeller motors.
Monfortex / Toptex
Additional “Classic Version” of the compressive shrinking unit at an attractive price-performance ratio.
Compactor
“Easy Compact” stentering field plus two drums felt compactor at attractive price-performance ratio; especially for knitted fabrics.
TexCoat coating unit
Optional CFK – coating roller for knife over roller processes for highest accuracy. Fully integrated plc controls.
Matex Allround
New padder module is exchangeable against coating module on the Matex Allround. Maximum flexibility of commission finishers.
Monforts Smart Order
New Internet platform (Webshop) for easily identifying and ordering wear & spare parts with user-friendly visualization (specific to the respective machine). Smart Support App
New Monforts app for direct communication of the customer to the Monforts service organization with new, advanced tools and functions to be used with smartphones (Chat, Video, White Board, Laser Pointer functionality, Telecon).
Fong’s ALC - Automatic Liquid Chemical Weighting and Dispensing System
The ALC Automatic Liquid Chemical Weighting and Dispensing System realizes unmanned dispensing according to the instructions fed from the Enterprise Resource Planning (ERP) system using advanced computer control technology. By means of precision mass flow-meter and metering pump, the liquid chemicals are accurately and precisely delivered and weighed from storage tanks, and with the application of valves and pipe network connections, the chemicals are accurately and rapidly distributed to the designated dyeing machine in the most effective way. With the efficient cleaning function after each delivery, not only is the operation efficiency of the dyeing plant improved but also it avoids human errors. Thus, dyeing quality is guaranteed.
XORELLA is ready for Industry 4.0
XORELLA has been a leading-edge manufacturer of equipment for conditioning and heat setting of textiles ever since the company was founded more than 50 years ago. The machines are renowned for their technology, operating efficiency and reliability.
For customers around the world XORELLA is the preferred partner for standard conditioning and heat-setting machines as well as for equipment for integration in fully automatic material handling and packing systems.
XORELLA has listened to customers’ input and reengineered the controller and its software. Latest generation hardware is used and software as well as visualization have been redesigned with a clear concept in mind: Easy operation even by less experienced staff in the mills.
There is a clear structure on all screens and the use of text was minimized. At the right side actual hazards are displayed with pictograms (such as high temperature in the picture below).
Handling and setting of the steaming programs was also simplified and programs can now be identified by alphanumeric names (max. 50 characters).
A new interface was created to assist customers in trouble shooting. Actual and historical data is saved and can be sent to our Service Department for analysis and support.
Paving the way for Big Data is the most important feature of the new XORELLA controller. It fully relies on its OPC UA interface for connection to external systems. Customers have the possibility to display the visualization on their own system completely by accessing the variables provided by the OPC UA. This considerably facilitates integration into superordinate systems. Therefore it is possible to link the XORELLA controller with process visualization systems provided by the main spinning machinery manufacturers or third parties.
You are invited to meet XORELLA’s team of specialists at booth in hall 6 at booth D203 to obtain detailed information on XORELLA machines and services.
Changzhou Hongda: Focusing on intelligent manufacturing
At ITMA 2019, Changzhou Hongda Technology Group is to focus on its Hawk Vision? intelligent image weft/pattern straightener.
Hawk Vision? Intelligent Image Weft/Pattern Straightener is an initiated internationally leading “full-width scanning pattern/weft straightening technology” of the brand “Hawk Vision” based on its strong European technology background and profound technology research and development ability of Changzhou Hongda. It adopts a completely new method, thoroughly solves pattern deformation, weft skewing and bowing of textile what the photoelectric weft straightening fails to identifying and straightening, Hawk Vision? Intelligent Image Weft/Pattern Straightener is suitable for yarn-dyed fabric, printing fabric, jacquard cloth, transfer printing fabric, sanding cloth, knitting, denim, sofa cloth, curtain cloth, twill, thick and heavy fabric, high count and density fabric, silk and imitation silk, chiffon, digital printing and sizing, compound processing with various kinds of weaving, breaks all limitations of the photoelectric weft straightener and common weft straightener against weaving kinds, texture, surpasses the value of the photoelectric weft straightening and common image weft straightening, thickness of fabrics and creates core value for textile enterprise.
The product was honorably awarded the First Prize for 2017 “Textile Vision” Technology Progress of China National Textile and Apparel Council and was appraised as the international leading level by the expert team of China National Textile and Apparel Council.
Atexco: Machine vision delivers precision
Atexco (Hangzhou Honghua Digital Technology Stock Co., Ltd.) specializes in the R&D, manufacturing sales and service of digital ink-jet printing technology and equipment.
Its products and solutions are widely used in the textiles printing, carpet printing and graphic printing industries worldwide.
Atexco was established in 1992 as a key company in the Software Park in the Hangzhou Hi-tech Zone and is a serial winner of the prestigious National Torch Prize. It also undertakes projects in the Hi-tech Research and Development Program (part of the government’s 863 plan) and the state’s High-tech Industrial Feasibility Project. Atexco is an international leader in garment CAD/CAM/ CIM systems, digital printing systems, inkjet direct manufacturing systems, advertising printing systems and carpet printing.
To date, precision digital textile printing has been seen in the form of garment shapes and individualized images printed on plain fabric, and more recently inkjet printing on thread has enabled precisely coloured embroidery. But precision is being taken one step further by Atexco’s new “machine-vision positioning printing” technology, which the company has said is a “revolutionary breakthrough in the existing digital textile printing field”, this new technology enables precision digital textile printing on woven fabrics, including lace, targeting specific areas with an injection of colour.
Whilst woven fabrics are rich in surface texture Atexco said, it is not possible to create the vivid colours that are available with printing, especially in half tone. And, digital textile printing enables garments to be produced in a very vivid colour pallet but lacks the depth of a weave. With this new technology, which harnesses “computer-vision technology,” Atexco’s machine vision positioning printing enables perfect matching between the print and the surface topography of the woven fabric, through on-time high resolution scanning, pattern recognizing, and manoeuvring. This technology overcomes the almost inevitable deformation of the fabric during processing, the company added. In the printing process, Atexco’s machine can quickly detect the intricacies of the lace, for example, and establish the precise positioning for the printing of each pattern. Discussing the details of the technology, Atexco said that it can align the print and fabric structure to a degree of accuracy within 0.2 mm, whilst printing at speeds of 90 sqm./h. As well as being suitable for lace, the technology can also be used in doublesided printing and for medium and heavy fabrics. When printing on medium weight and thick fabrics, whether printed by screen or digital printing, Atexco noted that the print cannot be realized fully on the back side of the fabric. However, double-sided printing is achieved through accurate positioning, the company said, and based on the machine vision technology, and its crucial software, Atexco’s new printer is able to accurately align the back side of a fabric for printing, after the printing of the front side.
This technology overcomes the deformation of the fabric that can occur, particularly when printing on the same substrate twice, Atexco said. For the direct double-sided printing, Atexco said it is accurate to less than 0.3 mm in terms of position matching accuracy. Not only this, but Atexco claims that this technology can also be used to realize bronzing effects on fabric. Traditional bronzing fabric can only be realized by screen printing. Jilong Machine: Focusing on high-precision rotary screen printing machine
At ITMA 2019, Fujian Jilong Machine Technologies Co., Ltd. will mainly focus on CD Rotary Screen Printing Machine and Jilong JFA Stenter Machine.
CD Rotary Screen Printing Machine is suitable for natural fiber, chemical fiber and blend fiber woven & knitted fabric printing. Open type screen head base design, magnet rod squeegee. Fabric weight range: 50 g/m2 - 600 g/m2.
Machine specification & technical parameters:
Printing Width Range: 1,650 mm - 3,250 mm;
Printing colors: 4 - 16 colors;
Printing repeat (mm): 640, 820 914 1018 1206;
Register Precision: ± 0.1 mm;
Printing Speed: 4 - 80 m/min;
Squeegee type: magnet or blade.
Jilong JFA Stenter Machine is suitable for cotton, poly/cotton, poly/viscose chemical fiber and blend fiber fabric, poly filament, DTY knitted fabric and other inter-texture stentering.
Technical parameters:
Machine Width: 180, 200, 220, 240, 260, 280, 300, 320 cm;
Fabric Width: 700 - (W-20) cm;
Machine Speed Range: 5 - 100 m/min;
Dryer highest working temperature: 220°C.
TPET: Mainly promoting four types of intelligent equipment
Suzhou Transparent Electronic Technology Co., Ltd. (TPET) will mainly recommend ET-5833 automatic terry towel machine, TPET intelligent home textile factory, ET-6660 automatic bed sheet machine, ET-5810 automatic microfiber towel machine, etc.
ET-5833 automatic terry towel machine has acquired 11 state-authorized patents of utility model. With the global origination of our full automatic terry towel machine, labor-saving and unmanned production process are achieved by the integration of cutting and sewing.
The productivity of this machine is 12,000 pcs/day (24 hours). The front part could save up to 6 labors, which means it will save around 54,000 USD/year. The rear part could save up to 7 labors which means it could save around 61,500 USD/year.
TPET intelligent home textile factory is a total solution of both software and hardware providing manufacture information, automation and intelligence. Through integrating automatic transport, automatic manufacture equipment, automatic testing equipment and information software, the platform realize data collection, monitoring, TPM equipment management, quality management, production scheduling and data analysis in the production, hereby the intelligent manufacturing management of information, intelligence and flexibility in all work sites. TPET first innovate the intelligent factory and put it into practice, having realized the automatic production for bed sheet, quilt cover, pillow cover, duvet, pillow inner; towels, bath towels, napkin towel, table napkin, hair-dry towel, dish towels; carpet, floor mat, blanket, curtain, bath curtain ect. Through the cloud management platform, we can help customers to understand the production efficiency of home textile intelligent factory in real time, the rate of finished products, the use efficiency of equipment, and the timely response to failure repair.
ET-6660 automatic bed sheet machine, labor-saving and unmanned production processes are achieved by the integration of cutting and sewing. Get everything done at one time for higher efficiency and less manpower including four-side hemming, fabric sewing, label-feeding and size-standardized. Has acquired 6 national authorized patents for utility models. It is applicable to the automatic production of standard-sized bed sheet.
With the global origination for ET-5810 automatic microfiber towel machine, label-saving and unmanned production processes are achieved by the integration of cutting and sewing. It has acquired 22 national authorized patents for utility models. It has wide scope to do the stitches like 3-thread over locking, 4-thread over locking, 2-needle 5 threads and 3-needle 6 threads over locking etc to promote the upgrading of factories.
Leadsfon Machinery: Exhibiting various series of circular knitting machine
Xiamen Leadsfon Machinery Co., Ltd. has been providing knitting machine and jointly developing several models with the world-famous Italian brand- Pilotelli since 2002. In 2014, Leadsfon acquired Pilotelli (China) and engaged top European technical as its consultants and the entire manufacturing process adopts European standard. Over the years, LEADSFON circular knitting machines have occupied in Europe and Southeast Asian countries including Indonesia, Vietnam, Thailand, as well as Turkey, Uzbekistan and so on.
Its products include single Jersey machine SJ series (such as SJ3.0, SJ3.0C-HS, JSP Terry Machine, FAC Three Yarn Fleece), double Jersey machine DJ series (such as DJC Interlock and rib knitting machine and DJI High feeders interlock knitting machine), high-tech products SINKERLESS DS3.0 series, etc.
Main features of DJC double knit machine
Designed with 1.8 - 2.4 feeds per diametrical inch with yarn guide ring;
Yarn guide seat can be adjusted dependently with three shafts, enhancing the reliability and durability of transmission system; Skid resistance of QUAP Pulley with belt, ensuring synchronization of yarn feeding wheel and reducing time of broken yarn;
Two adjusting buttons in dial and four adjusting buttons in cylinder in each cam box increase the adjustment range, facilitating the design change and adjustment accuracy;
The production of rib, interlock and design fabrics is more convenient, stable and efficient.
Main features of SJ3.0 HS single knit machine
It is proved by a long-term practice that the company has mature technology and wide range for customer to choose;
All accessories precision standardization are interchangeable, directly assembled into a machine;
Product structure reasonable compact, easy conversion;
High-quality materials, the most advanced technology refined processing of standard parts;
Its own patented dual steel wire runway can reduce friction, smooth operation, greatly enhance the speed;
Design and processing technology in line with CE standard;
Equilibrium angle;
Using special steel frame to balance the body during operation;
Having many patented technologies.
Main features of DS3.0 series
No more vertical line;
No more elastane misplating defects;
No more fabric peeling;
Ideal solution for fine gauges;
High productivity;
Solution of the problem of picking up the dropped-off fabric;
No more cleaning and maintenance operations needed;
Easy replacement of parts worn down by yarns;
Great energy saving. The energy saving is estimated at 10% - 15% compared to a machine with sinkers working under the same conditions.
Jingwei Intelligent Textile Machinery Co., Ltd.
At the exhibition, Jingwei Intelligent Textile Machinery Co., Ltd. will mainly promote its JWF1589 New high-speed intelligent series ring spinning machine.
JWF1589 ring spinning machine is a new high-speed intelligent series ring spinning frame developed by Jingwei Intelligent Textile Machinery Co., Ltd. according to the development trend of the current ring spinning machine with the existing mature technology and international advanced structure. The machine adopts modular and industrial integration design. Ring rail plate and yarn guide plate adopt active, stable and positive lifting system which can be equipped with electronic twisting, electronic drafting or mechanical drafting technology, and features of quick installation of entire section packing. Slub-yarn system, compact system, individual spindle broken-end detection system, roving feeding stop device and spandex core-spun yarn device are optional. The machine runs more stably and reliably at 22,000 - 25,000 rpm.
JWF1589 Composition of the machine: JWF1589 highspeed intelligent ring spinning frame with mechanical drafting and JWF1589E high-speed intelligent ring spinning machine with electronic twisting and electronic drafting
Advantages:
High speed in the entire section installation
The modular design of the entire installation technology makes the machine more stable at the speed of 22,000 - 25,000 rpm, and the installation time is greatly shortened.
Active and stable positive lifting system
Ring rail and the yarn guide plate adopt active and stable lifting system,which makes it more stable and reliable in the process of moving up and down at high speed and also avoids problem of ring rail gauge out for a long time.Spinning building is more perfect facilitating to high-speed winder and process parameters adjustment on the operation panel is more precise.
Electronic drafting
Servo-drivers are adopted instead of twist changing gear and total changing gear to realize processing parameter be adjusted on line, which widen the application scope of RSF spinning process. The Max. multiple is over 100 times. Rollers are controlled by high-precision servosystem through pulse follow technology to ensure roller driving synchronously. Energy-saving technology
Energy-saving motor,energy-saving spindle tape, energysaving tension device and energy-saving spindle are adopted.
Auto-doffing system
Stable auto-doffing system is adopted with high reliability.
Electronic twisting
The front roller speed can be adjusted automatically to ensure spindle running synchronously with roller and twist adjusted easily.
Compact spinning system (optional)
Integrated designed four roller compact system can improve yarn hairiness index.
Individual spindle broken-end detection device
Individual spindle speed, broken end, weak twist etc. can be detected precisely and yarn reserving rate, precise production etc. can be counted. And improve efficiency of spinning machine, reduce labor costs and promote operation ability.
Precise doffing-tube counting device
Counting convex disc without tube is fitted in the non-spinning position to avoid empty tube at doffing and reduce workload in winding process.
Electronic braking system
Precise yarn-end reserve, electronic braking and power interruption simultaneously can control brake motion rapidly and precisely, improve yarn reserving rate or avoid yarn-end cleaning. Electronic braking system is necessary for yarn clamping spindle.
Spinning technology expert system
Spinning technology one-key guide function: 10 sets of technology parameter are built in the program. The parameter can be invoked according to spinning varieties. Customer can revise or save the parameters convenient for the customer when changing spinning variety.
Continuous innovation of expanding functions:
Can be fitted with soft and smooth spinning unit and corespun yarn unit;
Roving-spinning combined and spinning-conner combined can be realized;
Colored yarn intelligent spinning controlling system;
On-line monitoring management network system;
Roving feeding stop system.
Beijing Jingwei Textile Machinery New Technology Co., Ltd.
Beijing Jingwei Textile Machinery New Technology Co., Ltd. will mainly exhibit its JWG0101 bobbin yarn automatic packaging system and JINLING (precise execution, flexible configuration) series of foreign fiber sorter.
JWG0101 bobbin yarn automatic packaging system is a full automatic bobbin yarn transportation and packaging system. The functions of automatic yarn loading, automatic transportation, yarn laying, automatic stacking, transplanting and transporting, stacking inspection, automatic film covering, bag opening and bagging, automatic sewing bag, weighing and labeling bag, automatic storage are realized. The automatic package system of bobbin yarn reduces more than 80% of the packaging workers, greatly reduces the labor cost and labor intensity of the employees, at the same time improves the work efficiency, reduces the production energy consumption, and improves the automation and intelligence level of the cotton spinning workshop. The bobbin yarn track conveying system completes taking yarn from the winder belt and conveying the bobbin yarn along the track to the automatic packaging area. The bobbin yarn is conveyed to the packaging area to lower the yarn and enter the automatic packaging line. The system is composed of lifting mechanism, track, suspension chain and yarn lowering mechanism.
The utility model is composed of a drum line and a shuttle truck, and is used for conveying drum yarn stacking and finished product stacking.
Main features:
Automatic yarn-feeding: from winder to air track automatically, and classify the types of memory yarn to realize automatic transport of yarn in air track;
Lower yarn arrangement: The yarn arrangement mechanism is dynamically allocated according to the number and variety of the bobbin yarn on the track to realize the automatic arrangement of the bobbin yarn on the track, and the weight of each bobbin yarn is measured in real time;
Automatic palletizing: automatic palletizing of bobbin yarn is realized by truss robot according to the variety of bobbin yarn;
Transplanting and transporting: the whole stacking yarn can be automatically transported to the packaging system through the drum line;
Palletizing inspection: realizing automatic palletizing and inspection of whole stacked yarn, and realizing inspection and elimination of yarn appearance;
Auto-sealing: realizing auto-covering and film-sealing of bobbin yarn;
Bag opening and bagging: automatic bagging of woven bags and automatic bagging of yarns;
Automatic sewing bags: full-bag drum yarn to achieve automatic sewing bags;
Weighing and labeling bags: automatic weighing, labeling and bundling of whole bag drum yarn;
Automatic warehousing: The whole bag of yarn is automatically coded and transported to the designated position by truss robot and AGV.
At present, it has been installed in Dasheng Textile Group, Nanyang Textile, Shandong Ruyi, Wuxi Longitudinal and Weft Textile Technology Testing Co., Ltd. and Wuxi Longitudinal and Weft Textile Technology Testing Co., Ltd. It has installed 50,000 spindles automatic transportation and packing system as the visiting workshop of this product. Welcome to visit and order from users.
JINLING (precise execution, flexible configuration) series of foreign fiber sorter is the automatic intelligent technology launched by Beijing Jingwei Textile Machinery New Technology Co., Ltd., which inherits the original technology accumulation, summarizes the user’s practical experience, absorbs the latest international technology, and independently innovates. Foreign fiber sorting equipment. He has more than 20 intellectual property rights to date. The equipment is suitable for installation in the process of cleaning and combing, clearing and winding, and ginning process. It can detect all kinds of foreign fibers in cotton in real time and high efficiency, including polypropylene fibers, flax fibers, hair, various color threads, plastic sheets,cloth pieces, polluted cotton, white polypropylene yarn and white threads, plastic films, etc.
The device uses artificial intelligence and large data processing to design recognition algorithms, parallel high-speed image processing architecture, multi-spectral illumination and imaging system (highlighted plastic films, no color, subtle features, etc.), high-speed and efficient ejection execution system (precise execution), Friendly human-machine interface, simple routine maintenance, remote operation and accessibility information collection system, modular selection (flexible configuration) according to customer characteristics. Since it was put on the market in 2003, more than 2,000 sets of equipment have been used to serve cotton spinning enterprises at home and abroad, which has become a powerful guarantee for the high quality of cotton spinning enterprises. The company solemnly promises: the products provide lifelong service, and the high-quality professional service team makes users feel more assured.
Yichang Jingwei Textile Machinery Co., Ltd.
Yichang Jingwei Textile Machinery Co., Ltd. is to exhibit its K3501 direct cabling corder. The series direct cabling corder is mainly used for making 2-ply symmetric tire cords and industrial yarns from the filament such as PA, PET, RAYON etc. this machine is characterized by low energy consumption, less labour, high quality tire cords and large packages. The tire cord can be used for making tire cord fabric, conveyor belt, driving belt, rope etc. It is also suitable for twisting all BCF yarns (PA, PP, PES, PTT, etc.), Continuous synthetic filament yarns (PA, PP, PES, PTT, etc.) , staple fibers, etc.
Main features:
High efficiency: Motor spindle drive, Max. mechanical speed is 11,000 rpm;
High quality: The patent new type cord regulator and hysteresis type inner yarn tensioner and outer yarn tensioner ensure the length consistent between inner yarn and outer yarns after spinning, and control the yarn tension more accurate. Accuracy tension control ensures the stable balloon, which results in high qualified twist;
Intelligent E-system: Realized the networking between machines, remote diagnosis and control; The Hi-lo creel adopt the new type pneumatic structure, easy to load and unload the feeding package;
Low power consumption: Stable outer yarn tension and balloon ensure the better e-saving effect;
Low strength loss: Improve the design of the yarn path parts to reduce the yarn strength loss;
Easy to threading operation by pneumatic method and quick to set the technical data;
High full package rate: Adopt the improved outer yarn tension intelligent control system, lower the yarn end breakage rate, further improve the full package rate;
The machine can be used as direct cabling and TFO twisting when twisting the carpet yarns, easy to change the production mode for the customer.
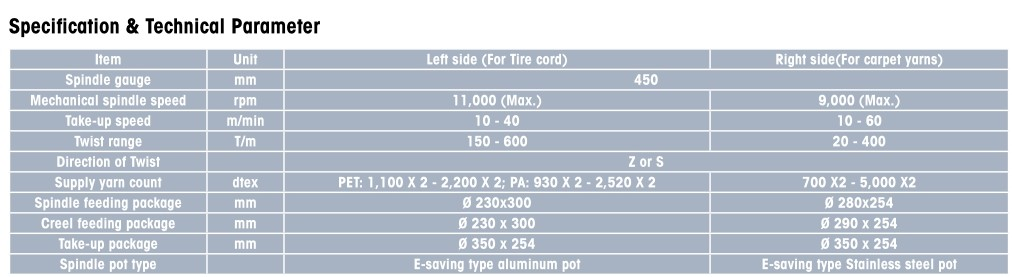
China Textile Science and Technology Co., Ltd.
China Textile Science and Technology Co., Ltd. is to exhibit its 3.2m SSS, 3.2m SMMS, and 3.2m SSMMS, providing you solution of spun-melt nonwovens equipment.
Specifications of 3.2m SSS:
Max. process speed: 600 m/min;
Max. output: 1,650 kg/h;
Weight scope: 8 - 80 gsm;
Fiber fineness: ≤ 1.6 den;
Power consumption per ton fabric: 700 - 900 kwh;
Weight coefficient of variation CV(%): ≤ 1 - 3%;
Elongation at break (%): ≤ 70%.
Specifications of 3.2m SMMS
Max. process speed: 600 m/min;
Max. output: 1,350 kg/h;
Weight scope: 10 - 80 gsm;
SB fiber fineness: ≤ 1.6 den;
MB fiber fineness: 2 - 5 μm;
Power consumption per ton fabric: 1,200 - 1,500 kwh;
Weight coefficient of variation CV(%): ≤ 1 - 3%;
Elongation at break (%): ≤ 75%;
Hydro head (mmH2O): ≥ 180 (13 gsm).
Specifications of 3.2m SSMMS
Max. process speed: 600 m/min;
Max. output: 1,900 kg/h;
weight scope: 10 - 80 gsm;
SB fiber fineness: ≤ 1.6 den;
MB fiber fineness: 2 - 5 μm;
Power consumption per ton fabric: 1,200 - 1,500 kwh;
Weight coefficient of variation CV(%): ≤1 - 3%;
Elongation at break (%): ≤ 75%;
Hydro head (mmH2O): ≥ 180 (13 gsm).
Rieter: Digital spinning as the key to success
Digital Rieter products have one thing in common: They are always focused on the customer. They not only help the decision-making process at management level, but also help employees take the numerous decisions that need to be taken every day in spinning mills, objectively and quickly. Digitalization is making inroads into spinning mills with Rieter Digital Spinning Suite, for example with SPIDERweb. This mill monitoring system records data on processes, quality and production efficiency, analyzes the data, and detects deviations promptly. This allows short response time to introduce the right measures, increases the efficiency of machinery, and reduces the cost of spinning mills. The system is also available for retrofitting on existing machines and equipment.
Rieter customers can monitor the performance of a spinning mill 24/7 from anywhere and respond quickly in critical cases with the Alert and Cock-pit Module for smartphones. It provides the key figures for production, quality and energy in real time.
Thanks to DASHboard, it is now possible to quickly and visibly display relevant key data in the mill. The display unit for spinning mills shows information on a range of factors, such as efficiency, production, quality, or the output of operators. In addition, the correlation between the factors can be shown, and predefined limit values can also be identified.
What if you knew exactly what actions needed to be taken be- fore a machine malfunctioned? With UPtime, the power of prediction is now available.
When it comes to machines and malfunctions, predicting the future could not only help a business avoid downtime, but could also save money, improve quality and increase productivity. Rieter introduces a new approach to machine maintenance with UPtime, an innovation that achieves what was once unimaginable: predicting issues and malfunctions before they happen.
The aim of any maintenance strategy is to minimize downtime and keep production on schedule. A preventive approach uses statistics to determine when maintenance should be executed, but this does not eliminate unexpected downtime and it can also lead to replacing parts before it is necessary to do so. Predictive maintenance is based on past and real-time data, which is analyzed to determine upcoming maintenance requirements.
UPtime collects data and uses artificial intelligence to identify the optimal time to perform maintenance based on a machine’s unique settings and usage. This can lead to cost savings by helping a business evade production interruptions and reduce its stock of spare parts.
Performance-critical information, such as air pressure, temperature and vibration, is transmitted to UPtime through sensors. This data is then used to detect behavior patterns related to potential machine failure. When these patterns occur, UPtime’s artificial intelligence recognizes the likelihood of failure and alerts technicians with early detection warnings and notifications about clear action steps. Furthermore, the system continuously learns from data and patterns, which means that UPtime’s predictive power improves over time. GERON Card Clothing: Exhibiting various products
At ITMA 2019, GERON Card Clothing (Jiangsu) Co., Ltd. brings a variety of products, including Flat top MCBH58, Flat top MCBH40/S, Flat top MCH52/B for Pima cotton, Flat top MCH52/M for superfine fiber, Double mountain cylinder wire AC2040B*1840, Integrate combing roller, 130 degree Circular comb, and Twin stationary flat.
Flat top MCBH58 is suitable for spinning high-impregnated cotton (machine cotton), medium and high 30 or more yarns for carding, combing, ring spinning, and air-jet spinning. Increasing horizontal density and reducing the working angle can improve carding for getting single fiber, less fiber damage, short fiber and neps. Through scientific distribution of the vertical direction, the needle angle can be improved, strengthening the control of the fiber combing flow direction, easy to clean trash and fiber less loading, improving the IPI.
Flat top MCBH40/S suits for synthetic fiber, especially better performance for polyester fiber (1.27-1.68dtex * 38mm). Optimized design to improve the carding and straighten fiber, fiber completely mix and carding; easily to remove the defect hard doubling fiber and less fiber damage. The wire structure and material is more suitable for high speed carding and have excellent performance to puncture fiber and release fiber, with better fiber control and less fiber loading.
Flat top MCH52/B for Pima cotton suits for carding U.S. Pima long cotton, solves the carding problem of increase short fiber and neps because of the high trash, high sugar, long length and thin fineness. It improves the wire life time and get the stability carding quality.
Flat top MCH52/M for superfine fiber is mainly for the carding differential fiber, the fine fiber. 6-1 dtex, less strength, low modulus of elasticity, much static, solve that produce neps because of the fiber easily twine during the carding.
Double mountain cylinder wire AC2040B*1840, according to the carding theoretical model, has the design philosophy: Increase one more small tooth on the back of the tooth, the small tooth will support the fiber and also carding fiber, improve the carding and improve the neps and trash remove efficiency. The sharp teeth design will keep the working surface smoothness, less influence for wire teeth wear resistance.
Integrate combing roller is produced by molding, avoided extra grooved, less intertwine. While working process, air more stable, and fiber transfer smooth, it can improve yarn CV. Through surface coated technology, it will make the roller surface smoother, decrease fiber damage and fiber transfer resistance. Due to diamond coated with high wear resistant, it makes DN coating roller longer life time than normal roller 3 to 5 times, it can reduce customer change roller times and yarn quality worse trouble. Convenience install and change while process different kind of yarn, reduce customer stock. High-precision processing ensures the sharpness, concentricity and consistency of all teeth height, it is high yarn quality effective guarantee. 130 degree Circular comb is featured with high speed & high production, high quality & low waste-cotton, and high spinnability. It suits for high speed and high production, the central angle increasing 18 degree base on 112 degree, it can satisfy the sliver weight 75 - 80 g/m, speed 450 - 500 nips/min high production combing machine. It satisfies customer’s high quality requirements.
Twin stationary flat construction suits for JSC326, JSC330(SC60), JWF1204, JWF1206, JWF1211, JWF1213, DK903, TC11, TC15, C60 high production carding machine, which use double rows wire (different PPSI), wire pitch and PPSI from thin to dense. Compared with the single product, the carding teeth are doubled to improve the carding effect and yarn quality.
Jiangyin Huafang: Displaying various equipment
During the exhibition, Jiangyin Huafang New Technology& Science Research Co., Ltd. is to exhibit various equipment, including HF928B high speed automatic sectional warping machine, HFGA158 Direct Warping Machine, HFGT158 Big V Creel, and HFGA136B Ball Warping Machine.
HF928R High Speed Automatic Sectional Warping Machine has wide applications, modular structures and lots of optional parts ensure this machine can warp any staple yarn and filament yarn. Main feature of this machine is the different winding direction which is winding counterclockwise, skein yarn can be put in without opening any roller when warping, guarantee a constant and complete arrangement of warp yarn. Accurate yarn guide motion is achieved by opening type between creel and front reed, without any skein ends. Fully usage of the evener roller (under warping table) guarantees the evenness of yarn section. According to different process when beaming, provide various types of yarn threading which reduce the friction between yarn and middle guide rollers. Beaming tension is controlled more stable by segmented. With displacement auto-measure system and section tension auto-control, computer workstation can store large amount of process parameters. Connecting with customer’s ERP data can be achieved and also connect with mobile APP to monitor machine working condition.
HFGA158 Direct Warping Machine is suitable working with cotton, hemp, polyester and blended fiber, etc... This machine applies Germany-imported encoder to count length, complete set of imported hydraulic components controls the pressure and brake force of press roller, provide guarantee for high efficient production and high quality products. When warping dyed beam, yarn feed roller is equipped with servo motor and laser system, which guarantees dyed beam meets customer’s process, and also equipped with servo controlled load/ unload system to work with different diameters of beam. Connecting with customer’s ERP data can be achieved and also connect with mobile APP to monitor machine working condition. HFGT158 Big V Creel is mainly workable for staple yarn over 32S and any specifications of cones. This creel applies original Switzerland SAURER broken yarn auto-stop detecting device, achieve individual broken yarn detecting, confirm yarn number preview. Auto pre-tensioner can prevent yarn loosen when machine stops, and automatically adjust to correct position according to different stages when warping, unique yarn tensioner guarantees low yarn tension when machine is working in high speed: internal individual blowing device keeps the tensioner clean, unique electric-cut device, cutter can be charged directly, no need other spare batteries.
HFGA136B Ball Warping Machine is workable for rope dyeing process in cotton industry. More user-friendly of load/unload, yarn threading control and vacuum device (dust-remove), unique press guarantees high quality ball, which can also reduce labor intensity and increase environment quality. Mechanical type and servo type of yarn feeding is optional for customers. Connecting with customer’s ERP data can be achieved and also connect with mobile APP to monitor machine working condition.
Ring frame electronic drive control: Simply ring frame constructure, cancel original main motor and wharve, so can remove the air flow influence caused by many wharve high speed running and reduce the noise. Spindle can drive seperately, set spinning twist directly, no need to change machinery parts and easy operation.Install the PCB board on keel, control each spindle running, easy erectionYarn breakage detection device, after yarn breakage, roving stop automatically, reduce waste, save energy sharply.
Qingdao Hicorp Group: Focusing on intelligent equipment
During the exhibition, Qingdao Hicorp Group will display a variety of production with original technologies, including HCP2025 Intelligent Roving Frame and Finished Woven Bags Automatic Packaging system.
The latest generation of intelligent roving Frame designed by Chinese and foreign experts team of Qingdao Hicorp Group for 10 years. The world’s first technology has subverted the traditional structure of the roving frame, broken through the bottleneck of the original structure, increased double spindles than original longest spindle (216 spindles) and made the operation more intelligent.
The main features:
The max spindle is up to 432 spindles;
Suitable for multi-varieties spinning;
The patent waste roving recycling system, recycling by variety, improve recycling efficiency; The electronic drafting, cancel all process gears;
Expert database system makes spinning easier;
Two different varieties can be spun at the same time, and the variety combination is more flexible;
Less area occupied, less labor requested;
Perfect connection between Hicorp Cloud and remote operation and maintenance system.
Finished Woven Bags Automatic Packaging system realizes unmanned automatic packaging. It has the function of automatic testing of bag pocket and automatic arrangement packing, which effectively solves the problem of automatic packaging with reliable sewing and compact filling of cone yarn.
The advantages:
Woven bag pattern: Finished woven bag;
Woven bag specifications: length ≤ 1,350, width ≤ 800;
Cone yarn arrangement: 3 * 4, 3 * 5, 2 * 4;
Bag load: Automatic;
Bag open: Automatic;
Bag support: Automatic;
Bag pocket finishing: Automatic;
Bag pocket sewing: Automatic;
Whole bag cone yarn delivery: Automatic;
Cone yarn arrange into bag: Automatic;
Yarn breakage check: Included;
Tight cone yarn bag arrange: Included.
Rizhao YUHUA Machinery: For high-quality component of textile, service forever
Rizhao YUHUA Machinery Co., Ltd. is to exhibit YUHUA brand series top arm, compact, and rings.
“YUHUA” brand top arm have been developed and produced since the end of 1980s. At present, it has achieved the sales of 30 million spindles in textile markets. YUHUA brand series top arm has four series of V-type draft, flat draft, compact spinning special top arm and spring arm. The pendulum arm has the characteristic of accurate pressure regulation, no spring fatigue, small spindle differences, high parallelism, excellent spinning. The product has large pressure regulation range, wide range of products suitable for spinning. The semi-release pressure canbe achieved during the holiday, no need to raise the arm, the rate of yarn breakage is lower when re-starting, high production efficiency.
“YUHUA” compact (be negative pressure four roller compact device) adopts special energy saving fan with low energy consumption. Open-type condensing system for easy maintenance. Torsion spring tension frame makes it easy to disassemble and assemble the lattice circle. The wear-resistant cover provides long service lift and convenient switching between normal spinning and siro spinning. The air flow reverse stop device is convenient for collective exhaust, preventing air flow from pouring backward, and avoiding the large area yarn breakage. The life of roller is double by shifting spinning technology. Cooperative clients (partly) include HENGFENG GROUP, SHANDONG DAHAI, SHANDONG HUAXING, SHANDONG RUYI, LIANFA TEXTILE, SANHE GROUP, CHANGSHAN, SHANDONG HONGYE, BROSS GROUP, HUAFU, YICHENG TIANSHU, XINJIANG XINTAI, etc. “YUHUA” brand rings are characterized by high precision, long life and short ripening period. There are 21 varieties of PG1 and PG1/2, with an annual production capacity of 5 million pieces.
In recent years, the company is committed to the research and development of high-end ring, the current production of high-precision is processed with CNC machine tools, with high dimensional accuracy, consistent internal and external organization and long service life, which is 3 - 5 times of ordinary steel ring, especially suitable for the production and application of compact spinning.
PINTER YUHUA China Technologies Co., Ltd.
At the exhibition, PINTER YUHUA China Technologies Co., Ltd. will showcase EffiSpin, Roving stop device, Spinning software management system, Core yarn, and Fancy spinning system.
Research and development, sales, service together with PINTER FANI, EffiSpin is divided into three series of cotton spinning, wool spinning, siro spinning - electromagnetic type and optical type. This device can collect data in real time, reduce labor, improve production efficiency, is the best choice for company to achieve fine management; it also supports the connection with internet to realize remote real-time monitoring, monitoring the running situation of each spindle; Effispin system used for cotton, Blumis used for wool and Star-Yarn Siro used for Siro.
Roving stop device can reduce roving waste and production labor, eliminate roller winding, reduce the accumulation of bellows, improve production environment, improve yarn quality, reduce energy consumption and save manufacturing cost.
S p i n n i n g software management system can monitor the r e a l - t i m e production infor-mation of the current shift of all machines, conduct data collation and analysis, and view various production data recorded and counted by the system, so as to make the management more reliable and more accurate.
Core yarn can precisely control the tension of the core yarn, automatic traverse,and reduce the loss of the rubber. Core yarn online monitoring can eliminate the empty core yarn and achieve efficient management and perfect control.
Fancy spinning system (come from PINTER CAIPO SAU) can input up to 6 different colors of yarn. Professional software system precisely controls and simulates the feeding of colored cotton yarns.
Brujas: To promote series of high-quality card clothing
Brujas Textile Tech (Shanghai) Co., Ltd. is a Sino-foreign joint venture manufacturer of card clothing. Brujas, founded in 1908 by the Brujas family in Terrassa Spain, has made a joint venture with White Shark Card Clothing Co., Ltd. since 2008. Brujas is a ISO9001 quality approved company and is known as a high quality card clothing product suitable for all carding applications. The main products coverage contains: metallic card clothing, flat tops, stationary flat, integral cylinder, combing roller, cleaning fillet, raising fillet etc., and they are widely used in the areas of cotton spinning, non-woven materials, wool and linen spinning.
In the past 100 years, Brujas has pursued the combination of industry and art, and has been committed to fine production of card clothing as well as the perfect protection of carding material.
Brujas can also provide related textile auxiliary equipment, for example: metallic wire mounting machine, metallic wire weld device, grinding machine, flat clipping machine, flat grinding machine, flat ends milling machine, high precision roller grinding machine, combing roller winding machine etc., and spare parts for textile machine.
Through years of cooperation with White Shark Card Cloth-
ing Co., Ltd., Brujas integrates the advantages in technology, equipment and resource, and produces high-grade card clothing in cooperation with White Shark.
Brujas makes arduous efforts to establish the domestic firstclass enterprise and promote the development of textile industry.
Brujas Textile Tech (Shanghai) Co., Ltd. will mainly recommend OE Wire & Rotor Spinning, Adjustable Stationary Flat, Metallic Card Clothing, Duplex Complete System of Stationary Flat, Flat Tops, etc.
The advantage of OE Wire & Rotor Spinning lies in super wear-resistant and long-life. The main characteristics of Adjustable Stationary Flatde are as follows: high wear-resistant, nonblocked, high anti-rolling, the tooth flatness is less than 0.05 mm, easy to install and adjust. The advantage of Metallic Card Clothing lies in soft combing to protect fiber, beneficial to improve the yarn strength.
Duplex Complete System of Stationary Flat is mainly featured by double rack to strengthen combing, special design with strong self-cleaning, and easy to install and adjust. Flat Tops are characterized by perfect combing channel and high removal efficiency of neps and impurities.
NYBELT CO.: Focusing on various belts and roller coverings
Jinan Tianqi Technical Belts Co., Ltd. (NYBELT CO.), founded in 1990, is one of the largest manufacturers of flat belts in the world. With the total investment of over US$40 million NYBELT possesses the world first-class production lines of nylon sheets, coating, rubber processing, calendering, laminating, leather-processing, transport bands, end-jointing and testing. NYBELT employs over 180 staff and workers including more than 70 of professionals and technicians, the core members of whom were systematically trained abroad both in theory and practice regarding flat belts production, research and development in belting technology, quality control, machinery operation and maintenance as well as after-service. NYBELT produces a wide range of high-efficiency transmission flat belts, tangential belts, spindle tapes, conveyor belts, roller coverings, transport bands, leather belts, nylon sheets and synchronous belts, which are widely used in textile machinery, paper-making, folder-gluer, graphic arts, wood-processing, leatherprocessing, food and tobacco processing, post sorting and others.
NYBELT’s products are popular not only in China but also abroad. It has become well known for providing excellence in service to the customers throughout the world. NYBELT name is backed by 24-hour-a-day service.
With the R&D center of state level, NYBELT has received numerous titles and awards for the progress and development in belting technology. Extensive research and development enables NYBELT continuously put out up-to-date products and keep its leading role in the trade.
NYBELT has gained the certificate of conformity of quality system certification and adopted ISO9001 Standard for its production and servicing of technical belts and nylon sheets.
At ITMA 2019, NYBELT CO. is to exhibit various products, including NYCO? transmission flat belts, NYCO? TE belts, and NYCO roller coverings.
NYCO? transmission flat belts structure consists of friction covers made of special synthetic rubber with high resistance to abrasion or chrome leather; nylon core layer of high tensile strength. Such structure enables the belt to have excellent comprehensive properties: Long service life; Transmission efficiency: over 98%; Transmission speed: over 60 m/s; Good flexibility and directionality; Good dimensional stability; Constant friction coefficient.
NYCO? TE belts are made up of super-high tensile strength PET fabrics and the best kinds of thermoplastic polymers, and the belt surface is component of XNBR with the high abrasion resistance and constant grip. So these TE belts have the characters of high efficiency, energy saving, outstanding dimensional stability, and long service life. They are widely used in various machineries with high speed and shorter tension devices, being unaffected by fluctuation ambient environment. NYCO? TE belts have been recognized by insides as one of the most excellent up to-date power transmission belts in world.
NYCO? roller coverings are designed for increasing coefficient of friction, which can be used in various processing stages of textile industry such as being used in water-jet, air-jet, rapier, projectile looms, fabric inspection machines and dyeing & printing machines by way of wrapping their fabric guide rollers. NYCO roller coverings have various kinds of surface textural designs. With the advantages of wear-resistance, no deformation, no longation, no stripping and durability they are designed for drawing all kinds of fabrics. Rifa Textile Machinery: Exhibiting four high-efficiency & low-consumption equipment
As a national key high-tech enterprise, Zhejiang Rifa Textile Machinery Co., Ltd. has always been market-oriented, focusing on the development of textile machinery technology, specializing in the production of textile machinery, and has successfully developed hundreds of products in four systems: twisting, spinning, weaving and knitting. Now it owns Shandong Rifa Textile Machinery Co., Ltd., Anhui Rifa Textile Machinery Co., Ltd. and Zhejiang Rifa Textile Machinery Technology Co., Ltd. At this exhibition, Rifa Textile Machinery will exhibit RS30D rotor spinning machine, crosrol cleaning comb, RFTL62 high-speed rapier towel loom, and RFJA40 high-speed air jet loom.
RS30D Rotor Spinning Machine
RS30D is an intelligent semi-automatically high-speed rotor spinning machine, integrated with technologies of a new advanced spinning unit, semi-automatic piecing device, automatic doffing, automatically cleaning spin box, Internet of things, electronic servo transverse and single independent drive, as well as electronic micro-switch etc. It opens a new world of semi-automatic air-flow spinning machine with higher production, lower power consumption and better user experience. Service anywhere anytime.
Crosrol Blowing-Carding
The equipment enjoys a balance between higher output and quality, featured with less space, low energy consumption, easy operation, and easy m a i n t e -nance. It is embodied in automatic repiece, automatic gauge adjustment, steel ball support, flat drive, short, medium and long auto-leveling, etc., with high cost performance.
RFTL62 High Speed Rapier Towel Loom
The device is directly driven by the new switched reluctance motor, consequently with an obvious power saving effect; the optimized conjugate cam tightening weft and the “space crankshaft and connecting rod” mechanism, with the new type weft insertion, greatly reducing the head and belt of rapier wear. The optimized towel let-off system ensures that the warp tension is the same, and the woolen loop is smooth and uniform.
RFJA40 High Speed Air-jet Loom
RFJA40 High Speed Air-jet Loom is characterized by highspeed and efficiency, energy saving and low consumption, high automation etc. With the lower center of gravity of the loom, the new dynamical balancing of beating-up mechanism effectively reduces the vibration of loom and at the same time the beating-up force is increased; the further optimization of the 4 - 6 connecting rod beating-up mechanism is more suitable for high speed weaving; the servo motor is used directly to drive the loom. It is obvious in energy saving and convenient for maintenance. Qingdao Haijia Machinery: Promoting three looms
Founded in 2001, Qingdao Haijia Machinery Co., Ltd. is a professional shuttleless looms manufacturing enterprise integrating R&D, manufacturing, sales, international trade and service.
The company attaches importance to the management of independent intellectual property rights, enjoying a total of 52 independent intellectual property rights.
In May 2019, the HW-8010 High-speed and High-density Water Jet Loom developed by the company passed the scientific and technological achievements appraisal. The experts agreed that the result is independent and innovative, and the overall technology has reached the international advanced level.
At ITMA 2019, Qingdao Haijia mainly promotes its HA9010-190-C6 High-speed Air Jet Loom, HW5012-190-P4 Water Jet Loom, and HW8010-230-D10 New High-speed and High-density Water Jet Loom.
HA9010-190-C6 High-speed Air Jet Loom is another new air jet loom developed by Haijia on the basis of HJA-N. The structure of left and right wallboard is beneficial to the production and manufacturing, so that the equipment will be more stable; Optimized design of the shape and position of the four supports makes the loom frame more stable; Improved beating mechanism makes the beating process more balanceable and stable during the operation. The structure of the back beam is improved to make the let-off more uniform and the tension more balanceable, which can reduce errors and improve the rate of high-quality production.
HW5012-190-P4 Water Jet Loom is deeply optimized on the basis of HW4010-190-P4, and the major improvements are: Multiple reinforcement measures are adopted for the machine to maintain a good stability during the high-speed and high-density weaving; Optimal design of weft insertion system improves the efficiency and can fit high-speed insertion; In the optimization of beating system, U shaped beating shaft and special beating balancing system are adopted. Solid beating shaft adopts reinforcement of supporting seat and centralized lubrication system, which improves the beating force and wear condition, increases the service life of the machine. This machine adopts servo direct drive motor, the energy saving effect can reach 25% - 30%.
HW8010-230-D10 New High-speed and High-density Water Jet Loom is deeply optimized on the basis of HW4012-190-P4, and the major improvements are: Adopt the integrated wallboard to optimize the design of the frame part, further improve the stability, efficiency and fabric quality; Reduce the height of the wallboard to make the operation of the loom more user-friendly; The beating method can be either four-bar or six-bar, which is suitable for different fabric requirements; Suitable for wide and high-density fabrics. Based on ultra-highspeed performance and designed with a maximum speed of 1,200 rpm/min, the machine is widely used in weaving fine denier, high-density and high-speed fabrics.
Niupai Textile Machinery: Promoting various shedding devices
At ITMA 2019, Niupai Textile Machinery will exhibit its NP4421 top-mounted positive shedding device, NP5400B highspeed electronic dobby, NP6016 electronic jacquard shedding device, and top-mounted high-speed positive cam shedding device.
NPW408D, whose frame box adopts integral structure, is top-mounted high-speed positive cam shedding device. With the property of strong rigidity, high manufacturing precision, excellent conjugacy, the device is equipped with U-shape steel beam and fully enclosed cover,which reinforces strength,safety as well as anti-corrosion performance and extends the service life of parts effectively. It can meet the weaving requirement of high speed and heavy duty fabric.
Technical Parameters
Reed space: 190 cm - 280 cm;
Max. RPM: 900 rpm (4/1weave, 190 reed space);
Heald frame spacing: 14 mm.
NP5600 Electronic Doddy is low-positioned intelligent positive shedding device that applies to wide and fast speed air-jet looms. Multiple cam curves are provided for weaving different fabrics. It’s characterized by its compact structure, easy operation and large capacity. Its oil filter can sift the fibers within housing.
Reed space: 190 cm - 360 cm;
Max. RPM: 750 rpm (190 cm reed space);
Heald frame spacing: 12 mm;
Shedding unit: 16 pcs;
Spec. of wire: 330 mm;
Shedding amount: 55 mm-160 mm;
Weft picks: 12800 picks.
NP5400B high-speed electronic dobby is top-mounted intelligent positive shedding device. The lubrication oil is forced to circulate via oil pump, and oil level sensor is adopted to avoid lacking oil. It’s characterized by compact structure and easy operation. Thus, it is especially suitable for fast speed and wide unbalanced fabrics. Its energy consumption is 1/3 less than mechanical dobby’s. The device is particularly popular among enterprises with fast changeover of fashion fabrics, short life-cycle and advanced technologies.
Technical Parameters
Reed space: 190 cm - 360 cm;
Max. RPM: 750 rpm (190 cm reed space).
NP6016 electronic jacquard shedding device features longitudinal arrangement of 16 lines of components. With the advantages of compact structure, light weight and robustness, the device can meet the needs of high speed running. NP6016 is equipped with electrical self-check function. It’s capable of weaving tie, trademarks, towels, clothing fabric and lining. Technical Parameters
Specification: 1408, 2816, 3072, 4096, 5120, 5376;
Max RPM: 650 rpm (based on process of fabric weave);
Shedding amount: 46 mm - 130 mm;
Full load of hook ≤ 2,000 kg.
Wuxi Hongyuan: Focusing on high-speed intelligent products
Wuxi Hongyuan Electromechanical Technology Co., Ltd. is highlighted on various intelligent products, including HY-9 Automatic Doffing High-Speed Draw Texturing Machine, HY-10 Multi-Spindle High-Speed Draw Texturing Machine, HY-Auto498 Auto Doffing Roving Frame, and HY-IDS Synthetic Filament Bobbin Automatic Handing System.
HY-9 Automatic Doffing High-Speed Draw Texturing Machine has the characteristics of high automatic level, energy saving, high speed and efficiency, easy operation, etc.
It is featured with total 384 spindles per machine, multi spindles, large production output capacity. Take-up device lies both sides of the machine, easy for operation and maintenance. Pneumatic yarn threading device can make sure the yarn threading performance accurately and labor saving as well. Motorizing friction unit, bobbin auto-doffing device, Hongyuan advanced take-up device.
Developed with multi-function, energy saving, easy operation and high efficiency, with independent intellectual property rights, HY-10 Multi Spindles Draw Texturing Machine can meet the current fierce market competition, and lead the fancy yarn making market. Machine capacity and efficiency are doubled.
Under same spindles, this machine area can shorten half of the space, and reduce the investment.
To achieve High Efficiency and Energy saving, High Automation, reduce labor employment and labor intensity, and satisfy the requirement of high level customer, Hongyuan company developed a new model roving frame with Auto Doffing — HYAuto498. The drafting and main drive system maintain the stable and reliability of the mature machine of Hongyuan company. With external auto-doffing structure, automatically fulfil bobbin doffing, bobbin exchange, yarn threading, run the machine. For the whole process, it needs around 2 minutes.
The characteristics of HY-Auto498 Auto doffing Roving Frame include: With reasonable machine layout reliable headstock driving, easy operation, suitable for high speed. Adopt mature control system and driving mode for 4 main drive and drafting system. Auto-doffing structure adopts external whole doffing design combined with double direction-freedom bobbin rail. Auto-doffing time is not limited by the spindle number, around 2 minutes with high efficiency. With multi inverters control synchronously, the auto doffing rate, empty bobbin exchange rate and auto yarn threading rate can reach nearly 100%, reducing at least half of the labor force. With Touch screen as HMI, easily for input technical parameters and yarn tension control and adjust, doffing parameters can adjust flexibly according to user’s requirement. The automatic bobbin doffing and transport system developed by Hongyuan is a special automatic bobbin-handling system for chemical filament yarn production line.
This system can realize the functions of bobbin auto-doffing and transportation. It can improve the automation level of subsequent process of chemical filament yarn production, improve the product quality and reduce the labor cost. To personalized auxiliary filament yarn product automation system, the module can combine freely according to the different requirement. This system has the characteristics of high quality, high efficiency and lower cost and achieve the international advanced level.
Cixing “KNIT TO SHAPE”opens a new textile future
As the world’s leading intelligent knitting equipment solution provider, Cixing will present a milestone design for the industry - KS series “KNIT TO SHAPE” computerized flat knitting machine, at ITMA 2019 in Barcelona, Spain, which will take you into a new world of knitting. Through the “KNIT TO SHAPE” computerized flat knitting machine and sweater automatic stitching linking system to achieve the machine replacement, and supplemented by the information system to transform the traditional production mode to achieve the division of labor across the entire industry chain. Create a C2M, C2B2C win-win ecosystem for the international knit sweater and footwear market.
“KNIT TO SHAPE” is a new type of fully automatic computerized flat knitting machine developed for ten years by the engineers of Ningbo Cixing Co., Ltd. and its subsidiary, Steiger, Switzerland. It brings together the wisdom of the current knitting technology research and development team, uses intelligent manufacturing, intelligent technology and intelligent knitting as the three carriers, and realizes the knit to shape. It eliminates the expensive, timeconsuming and posterior suture, realizes the automatic knitting, and presents the frontier development trend of current computerized flat knitting machine technology with great technological innovation.
The one-yard to shape technology of KNIT TO SHAPE computerized flat knitting machine can simultaneously complete the knitting of the whole sweater and exhibit it directly to the customer in three-dimensional way. This technology eliminates the costly and time-consuming process of linking, which can achieve the “what you see is what you get” knitting of the real 3D programming, making the production more flexible, more efficient, and the coil is more perfect. About Cixing
Ningbo Cixing Co., Ltd. (stock code: 300307) is a leading company in the world’s supplier of intelligent knitting machinery, and the national high-tech enterprise that is committed to improving the level of China’s knitting machinery technology, promoting the development of knitting technology progress, and realizing knitting industry upgrading.
Cixing shares were successfully listed in 2012, the only listed company in the computerized flat knitting machine industry in China, and Cixing has many advanced patents, of which, a number of technologies to reach the international advanced level, the level of product technology and quality has always maintained the forefront of the industry. Cixing shares have more than 10 subsidiaries, the innovative R&D products include computerized flat knitting machine, Intelligent Flat Knitting Machine, fully automatic stitching system, automatic ironing machine, industrial robots, service robots, Cixing is a representative enterprise of China’s intelligent equipment.
CHTC FONG’S creates a new era of smart dyeing & finishing
CHTC Fong’s has been committed to the development and manufacturing of dyeing and finishing equipment for more than 50 years. In the past decades, CHTC Fong’s devoted to the development of energy-saving and emission reduction machines and now it becomes the basic conditions for dyeing factories. At ITMA 2019 in Barcelona, Spain from June 20th to 26th, CHTC FONG’S will exhibit a full line of the most advanced and innovative products and technology including the new product- FONG’S TECWIN High Temperature Dyeing Machine, Fong’s ALC - Automatic Liquid Chemical Weighting and Dispensing System, THEN SMARTFLOW, Goller KINT MERC, MONNFONG’s Matex Eco Applicator, XORELLA, and MONFORTS Montex Stenter.
FONG’S TECWIN High Temperature Dyeing Machine
FONG’S TECWIN is designed to satisfy the ever-changing market demands. The reliability and versatility of the machine are improved.
TECWIN is equipped with several patented designs:
Combined Air and Front Spray Nozzle
Standard Feature: Increase the degree of dye liquor interchange before passing through the main nozzle.
Optional Feature: Optional blower is equipped. High pressure aerodynamic flow in spray nozzle is provided to resolve the special fabrics that demand high quality.
Automatic Adjustable Nozzle
Adjustment of nozzle setting is automatically done by means of motor drive system, and hence manual changing of nozzle is not required. Liquor Dispersion Storage Chamber
This is a uniquely design chamber for providing a better liquor dispersion effect.
Upper and Lower Overflow
Lower Overflow: Maintaining pump operation with low water level to prevent disturbance caused by rinsing at a high water level;
Upper Overflow: This is adopted for conventional overflow rinsing function.
Furthermore, the dye liquor separation is specially designed in TECWIN. With the use of the variable loading storage chamber, the dyeing operation can be performed more smoothly and fabric patterns can be more organized, which eventually leads to a lower liquor ratio.
The THEN SMARTFLOW– setting a new standard in jet dyeing
At ITMA 2019 in Barcelona from June 20th - 26th, FONG’S EUROPE, a member of CHTC FONG’S international Group based in Schw?bisch Hall, Germany, will introduce its THEN SMARTFLOW TSF hydraulic high temperature dyeing machine.
The THEN SMARTFLOW TSF is designed to achieve the lowest possible energy and water consumption rates available on the market for jet dyeing, with achievable liquor ratios for a full load up to 300 kg with a reduced kier volume and a liquor ratio down to 1:3.5 for cotton and 1:2.5 for synthetics.
FONG’S EUROPE has a number of patents pending on the innovative new features of this machine, including the SMARTFLOW’s fabric transport design. This is based on a smart, winchless fabric transport system which eliminates the need for a loading rope, and a circular plaiter with programmable rotation speeds which provides full filling of the drop zone.
The chambers can accommodate variable loads in terms of both weight and material type down to 40 kg for extremely flexible processing, and each SMARTFLOW TSF unit can be equipped with up to 8 chambers, in order to fully maximize productivity, while taking up to 40% less floor space than competing systems.
“The newly-developed nozzles and reel-less transport in combination with smart controlled circular plaiting and variable chamber adjustment provide even fabric treatment without en- tanglements and the highest loading capacity with the lowest kier volume,” explains FONG’S EUROPE Sales and Marketing Director Richard Fander.
Another innovation is the new bath preparation unit (BPU) and its patented satellite tank.
“As the process times of jet machines have been continuously optimised over the past few decades, they have required an increasing number of service tanks for dyes, auxiliaries and hot water, adding both expense and additional space requirements,” says Mr. Fander. “Our new BPU and satellite tank, with its automatic dosing and mixing programmes, working in combination with the THEN temperature management system, ensures the recipes are supplied in exact quantities, with dyes and auxiliaries well diluted and heated to the required temperature extremely rapidly.” “The new THEN SMARTFLOW allows fully reproducible processing with the optimized use of raw materials, water and energy, for perfect dyeing every time,” he concludes. “Hydraulically driving the fabric without the use of a transport winch opens the door to reducing the tension during treatment and results in the highest relaxation of stretch and spandex fabrics.”
FONG’S EUROPE will be at stand D101 in Hall 2 at ITMA 2019 with THEN and Goller, and Xorella will be at stand D203 in Hall 6.
GOLLER“GOLLER KNIT MERC”
Goller new knit mercerizing was developed to achieve highest quality mercerizing of knit fabrics with lowest tension and upmost best dimension stability (< 3%) over the fabric width for perfect dyeing results.
This new mercerizing compartment is the result of our consequent R&D developments and follow up of our latest “SINTENSA CYCLONE” drum washing compartments for highest washing efficiency with lowest tension.
Fabric content 8,4 mtr. in impregnation compartment plus 4 mtr. in first chain section which gives a production speed of 25 m/min by 30 sec dipping time.
Dry on wet mercerizing;
Cold or hot mercerizing;
Inlet with scroll roller and slat roller for fabric guidance;
Tandematic uncurler in front of rubberized de-airing roller;
Grooved bottom roller with 320mm;
600mm perforated upper drums;
Automatic tension regulation;
Low liquor content integrated lye tank with circulation and Auto filter;
8ton high efficiency squeezer on exit before chain section;
Cast iron pin chain with edge sensors, Tandematic un-curler and overfeed device;
Driven belt arrangement for fabric support;
Overflow wires incl. circulation and filtering for stabilizing;
5ton squeezer at exit of chain field;
High efficiency Goller “SINTENSA CYCLONE” drum washing compartment with Cyclone Rotor specially designed to create an adjustable under-pressure, for an optimized fabric transport, highest washing efficiency and minimized elongation.
MONFORTS FONG’s Matex Eco Applicator
The conventional process of drying the fabric with wet pick up in Stenter process will cause large heat energy consumption, particularly it needs to heat up and evaporate water from the fabric. Our Eco-Applicator will be different from the tradition way but to be the solution to save the energy from this part of processing.
Minimum liquor application device with driven liquor rollers. The alternative to padding. For energy-conscious and cost-cutting drying. Reduced liquor content for lower remaining liquor in the trough. Universal application: Liquor application to one or two sides or different liquor application on front and reverse side. Applications:
Application of softener for terry fabric;
Over dyeing or finishing of denim fabrics;
Hydrophobing/hydrophiling professional clothing;
Stain-repellent finish of decoration fabrics;
Functionalising (e.g. anti-smell) of outerwear;
Eco Applicator for Knitwear and bi-elastane Woven.
Eco Applicator could be suitable for Knitwear and bi-elastic Wovens.
Technical facts:
Suitable for “wet-in-wet and “dry-in-wet” process;
Permanent fabric weight control;
Add on precisely adjusted based on real fabric weight;
Defined application of e.g. softener;
Reproducible effects;
Same or less chemical consumption;
Less wet pick up – less heating energy required;
Contribution to lowering carbon footprint;
Patent applied system – unique selling point.
MONFORTS Montex Stenter with new improved features
New patented sealing devices at inlet and outlet Monforts“bionic fin?” for less heat loss and improved energy efficiency;
New integrated, modular “Eco Pack” unit for individual configuration with heat recovery module, exhaust air cleaning module, UV-zone module for odor remove. For achieving no visible smoke coming out of the stack;
New energy improved stenter design measures with improved sealing of the chamber and preheating of the combustion air option. All measures together lead to overall reduced energy consumption of the app. 13% (depending on the process);
Smart sensors in the stenter allow monitoring of the complete machine by digital twin. Maintenance can be further optimized and productivity improved: Smart sensors for grease reservoir filling of the stentering chain, Smart sensors for wear of Chain rails, spindles and impeller motors.
Monfortex / Toptex
Additional “Classic Version” of the compressive shrinking unit at an attractive price-performance ratio.
Compactor
“Easy Compact” stentering field plus two drums felt compactor at attractive price-performance ratio; especially for knitted fabrics.
TexCoat coating unit
Optional CFK – coating roller for knife over roller processes for highest accuracy. Fully integrated plc controls.
Matex Allround
New padder module is exchangeable against coating module on the Matex Allround. Maximum flexibility of commission finishers.
Monforts Smart Order
New Internet platform (Webshop) for easily identifying and ordering wear & spare parts with user-friendly visualization (specific to the respective machine). Smart Support App
New Monforts app for direct communication of the customer to the Monforts service organization with new, advanced tools and functions to be used with smartphones (Chat, Video, White Board, Laser Pointer functionality, Telecon).
Fong’s ALC - Automatic Liquid Chemical Weighting and Dispensing System
The ALC Automatic Liquid Chemical Weighting and Dispensing System realizes unmanned dispensing according to the instructions fed from the Enterprise Resource Planning (ERP) system using advanced computer control technology. By means of precision mass flow-meter and metering pump, the liquid chemicals are accurately and precisely delivered and weighed from storage tanks, and with the application of valves and pipe network connections, the chemicals are accurately and rapidly distributed to the designated dyeing machine in the most effective way. With the efficient cleaning function after each delivery, not only is the operation efficiency of the dyeing plant improved but also it avoids human errors. Thus, dyeing quality is guaranteed.
XORELLA is ready for Industry 4.0
XORELLA has been a leading-edge manufacturer of equipment for conditioning and heat setting of textiles ever since the company was founded more than 50 years ago. The machines are renowned for their technology, operating efficiency and reliability.
For customers around the world XORELLA is the preferred partner for standard conditioning and heat-setting machines as well as for equipment for integration in fully automatic material handling and packing systems.
XORELLA has listened to customers’ input and reengineered the controller and its software. Latest generation hardware is used and software as well as visualization have been redesigned with a clear concept in mind: Easy operation even by less experienced staff in the mills.
There is a clear structure on all screens and the use of text was minimized. At the right side actual hazards are displayed with pictograms (such as high temperature in the picture below).
Handling and setting of the steaming programs was also simplified and programs can now be identified by alphanumeric names (max. 50 characters).
A new interface was created to assist customers in trouble shooting. Actual and historical data is saved and can be sent to our Service Department for analysis and support.
Paving the way for Big Data is the most important feature of the new XORELLA controller. It fully relies on its OPC UA interface for connection to external systems. Customers have the possibility to display the visualization on their own system completely by accessing the variables provided by the OPC UA. This considerably facilitates integration into superordinate systems. Therefore it is possible to link the XORELLA controller with process visualization systems provided by the main spinning machinery manufacturers or third parties.
You are invited to meet XORELLA’s team of specialists at booth in hall 6 at booth D203 to obtain detailed information on XORELLA machines and services.
Changzhou Hongda: Focusing on intelligent manufacturing
At ITMA 2019, Changzhou Hongda Technology Group is to focus on its Hawk Vision? intelligent image weft/pattern straightener.
Hawk Vision? Intelligent Image Weft/Pattern Straightener is an initiated internationally leading “full-width scanning pattern/weft straightening technology” of the brand “Hawk Vision” based on its strong European technology background and profound technology research and development ability of Changzhou Hongda. It adopts a completely new method, thoroughly solves pattern deformation, weft skewing and bowing of textile what the photoelectric weft straightening fails to identifying and straightening, Hawk Vision? Intelligent Image Weft/Pattern Straightener is suitable for yarn-dyed fabric, printing fabric, jacquard cloth, transfer printing fabric, sanding cloth, knitting, denim, sofa cloth, curtain cloth, twill, thick and heavy fabric, high count and density fabric, silk and imitation silk, chiffon, digital printing and sizing, compound processing with various kinds of weaving, breaks all limitations of the photoelectric weft straightener and common weft straightener against weaving kinds, texture, surpasses the value of the photoelectric weft straightening and common image weft straightening, thickness of fabrics and creates core value for textile enterprise.
The product was honorably awarded the First Prize for 2017 “Textile Vision” Technology Progress of China National Textile and Apparel Council and was appraised as the international leading level by the expert team of China National Textile and Apparel Council.
Atexco: Machine vision delivers precision
Atexco (Hangzhou Honghua Digital Technology Stock Co., Ltd.) specializes in the R&D, manufacturing sales and service of digital ink-jet printing technology and equipment.
Its products and solutions are widely used in the textiles printing, carpet printing and graphic printing industries worldwide.
Atexco was established in 1992 as a key company in the Software Park in the Hangzhou Hi-tech Zone and is a serial winner of the prestigious National Torch Prize. It also undertakes projects in the Hi-tech Research and Development Program (part of the government’s 863 plan) and the state’s High-tech Industrial Feasibility Project. Atexco is an international leader in garment CAD/CAM/ CIM systems, digital printing systems, inkjet direct manufacturing systems, advertising printing systems and carpet printing.
To date, precision digital textile printing has been seen in the form of garment shapes and individualized images printed on plain fabric, and more recently inkjet printing on thread has enabled precisely coloured embroidery. But precision is being taken one step further by Atexco’s new “machine-vision positioning printing” technology, which the company has said is a “revolutionary breakthrough in the existing digital textile printing field”, this new technology enables precision digital textile printing on woven fabrics, including lace, targeting specific areas with an injection of colour.
Whilst woven fabrics are rich in surface texture Atexco said, it is not possible to create the vivid colours that are available with printing, especially in half tone. And, digital textile printing enables garments to be produced in a very vivid colour pallet but lacks the depth of a weave. With this new technology, which harnesses “computer-vision technology,” Atexco’s machine vision positioning printing enables perfect matching between the print and the surface topography of the woven fabric, through on-time high resolution scanning, pattern recognizing, and manoeuvring. This technology overcomes the almost inevitable deformation of the fabric during processing, the company added. In the printing process, Atexco’s machine can quickly detect the intricacies of the lace, for example, and establish the precise positioning for the printing of each pattern. Discussing the details of the technology, Atexco said that it can align the print and fabric structure to a degree of accuracy within 0.2 mm, whilst printing at speeds of 90 sqm./h. As well as being suitable for lace, the technology can also be used in doublesided printing and for medium and heavy fabrics. When printing on medium weight and thick fabrics, whether printed by screen or digital printing, Atexco noted that the print cannot be realized fully on the back side of the fabric. However, double-sided printing is achieved through accurate positioning, the company said, and based on the machine vision technology, and its crucial software, Atexco’s new printer is able to accurately align the back side of a fabric for printing, after the printing of the front side.
This technology overcomes the deformation of the fabric that can occur, particularly when printing on the same substrate twice, Atexco said. For the direct double-sided printing, Atexco said it is accurate to less than 0.3 mm in terms of position matching accuracy. Not only this, but Atexco claims that this technology can also be used to realize bronzing effects on fabric. Traditional bronzing fabric can only be realized by screen printing. Jilong Machine: Focusing on high-precision rotary screen printing machine
At ITMA 2019, Fujian Jilong Machine Technologies Co., Ltd. will mainly focus on CD Rotary Screen Printing Machine and Jilong JFA Stenter Machine.
CD Rotary Screen Printing Machine is suitable for natural fiber, chemical fiber and blend fiber woven & knitted fabric printing. Open type screen head base design, magnet rod squeegee. Fabric weight range: 50 g/m2 - 600 g/m2.
Machine specification & technical parameters:
Printing Width Range: 1,650 mm - 3,250 mm;
Printing colors: 4 - 16 colors;
Printing repeat (mm): 640, 820 914 1018 1206;
Register Precision: ± 0.1 mm;
Printing Speed: 4 - 80 m/min;
Squeegee type: magnet or blade.
Jilong JFA Stenter Machine is suitable for cotton, poly/cotton, poly/viscose chemical fiber and blend fiber fabric, poly filament, DTY knitted fabric and other inter-texture stentering.
Technical parameters:
Machine Width: 180, 200, 220, 240, 260, 280, 300, 320 cm;
Fabric Width: 700 - (W-20) cm;
Machine Speed Range: 5 - 100 m/min;
Dryer highest working temperature: 220°C.
TPET: Mainly promoting four types of intelligent equipment
Suzhou Transparent Electronic Technology Co., Ltd. (TPET) will mainly recommend ET-5833 automatic terry towel machine, TPET intelligent home textile factory, ET-6660 automatic bed sheet machine, ET-5810 automatic microfiber towel machine, etc.
ET-5833 automatic terry towel machine has acquired 11 state-authorized patents of utility model. With the global origination of our full automatic terry towel machine, labor-saving and unmanned production process are achieved by the integration of cutting and sewing.
The productivity of this machine is 12,000 pcs/day (24 hours). The front part could save up to 6 labors, which means it will save around 54,000 USD/year. The rear part could save up to 7 labors which means it could save around 61,500 USD/year.
TPET intelligent home textile factory is a total solution of both software and hardware providing manufacture information, automation and intelligence. Through integrating automatic transport, automatic manufacture equipment, automatic testing equipment and information software, the platform realize data collection, monitoring, TPM equipment management, quality management, production scheduling and data analysis in the production, hereby the intelligent manufacturing management of information, intelligence and flexibility in all work sites. TPET first innovate the intelligent factory and put it into practice, having realized the automatic production for bed sheet, quilt cover, pillow cover, duvet, pillow inner; towels, bath towels, napkin towel, table napkin, hair-dry towel, dish towels; carpet, floor mat, blanket, curtain, bath curtain ect. Through the cloud management platform, we can help customers to understand the production efficiency of home textile intelligent factory in real time, the rate of finished products, the use efficiency of equipment, and the timely response to failure repair.
ET-6660 automatic bed sheet machine, labor-saving and unmanned production processes are achieved by the integration of cutting and sewing. Get everything done at one time for higher efficiency and less manpower including four-side hemming, fabric sewing, label-feeding and size-standardized. Has acquired 6 national authorized patents for utility models. It is applicable to the automatic production of standard-sized bed sheet.
With the global origination for ET-5810 automatic microfiber towel machine, label-saving and unmanned production processes are achieved by the integration of cutting and sewing. It has acquired 22 national authorized patents for utility models. It has wide scope to do the stitches like 3-thread over locking, 4-thread over locking, 2-needle 5 threads and 3-needle 6 threads over locking etc to promote the upgrading of factories.
Leadsfon Machinery: Exhibiting various series of circular knitting machine
Xiamen Leadsfon Machinery Co., Ltd. has been providing knitting machine and jointly developing several models with the world-famous Italian brand- Pilotelli since 2002. In 2014, Leadsfon acquired Pilotelli (China) and engaged top European technical as its consultants and the entire manufacturing process adopts European standard. Over the years, LEADSFON circular knitting machines have occupied in Europe and Southeast Asian countries including Indonesia, Vietnam, Thailand, as well as Turkey, Uzbekistan and so on.
Its products include single Jersey machine SJ series (such as SJ3.0, SJ3.0C-HS, JSP Terry Machine, FAC Three Yarn Fleece), double Jersey machine DJ series (such as DJC Interlock and rib knitting machine and DJI High feeders interlock knitting machine), high-tech products SINKERLESS DS3.0 series, etc.
Main features of DJC double knit machine
Designed with 1.8 - 2.4 feeds per diametrical inch with yarn guide ring;
Yarn guide seat can be adjusted dependently with three shafts, enhancing the reliability and durability of transmission system; Skid resistance of QUAP Pulley with belt, ensuring synchronization of yarn feeding wheel and reducing time of broken yarn;
Two adjusting buttons in dial and four adjusting buttons in cylinder in each cam box increase the adjustment range, facilitating the design change and adjustment accuracy;
The production of rib, interlock and design fabrics is more convenient, stable and efficient.
Main features of SJ3.0 HS single knit machine
It is proved by a long-term practice that the company has mature technology and wide range for customer to choose;
All accessories precision standardization are interchangeable, directly assembled into a machine;
Product structure reasonable compact, easy conversion;
High-quality materials, the most advanced technology refined processing of standard parts;
Its own patented dual steel wire runway can reduce friction, smooth operation, greatly enhance the speed;
Design and processing technology in line with CE standard;
Equilibrium angle;
Using special steel frame to balance the body during operation;
Having many patented technologies.
Main features of DS3.0 series
No more vertical line;
No more elastane misplating defects;
No more fabric peeling;
Ideal solution for fine gauges;
High productivity;
Solution of the problem of picking up the dropped-off fabric;
No more cleaning and maintenance operations needed;
Easy replacement of parts worn down by yarns;
Great energy saving. The energy saving is estimated at 10% - 15% compared to a machine with sinkers working under the same conditions.